LIVE CHAT WITH THE INJECTION MOULDING MACHINE
The application "socialProduction" turns machines into team members.
What emoticons would a production machine use - 0/1 for a shoulder shrug? A ticking dollar clock when a line stoppage is imminent? For graphic designers and engineers, the topic offers potential to develop creative ideas together. After all, we are communicating with software assistants and "smart" machines in more and more areas of life. And at some point, they will no longer respond with bulky text modules and selection menu logic in the work environment, but rather fluidly and helpfully like their colleagues.
Chat rooms in which humans and machines exchange information about unit numbers, performance information or shift changes with each other like in a WhatsApp group are already available: "socialProduction", a mobile app and web application for injection molding machines from KraussMaffei, combines the advantages of social media with production monitoring technologies. In secure chat rooms, the machines report live events and problems that they detect independently in the production process. Since users can exchange texts and images in the chat, the machine is quickly perceived as an "active team member" in production.
As a digital production tool, "socialProduction" thus addresses several needs in the industry: The application improves the flow of information about machine availability and scrap rates, reduces the number of paper-based work steps and thus the error rate in the demanding injection molding process - and does so worldwide and around the clock on common devices.
Algorithm with plastics know-how
With two performance modules - production monitoring and process support - "socialProduction" is precisely tailored to the needs of users in plastics production:
Process support
Using a self-learning process based on AI/machine learning technologies, all available process parameters of the machine are continuously monitored. Here, KraussMaffei's plastics process knowledge has been incorporated into the programming of a patented algorithm that forms the core of the software.
An anomaly detection identifies abnormalities in the manufacturing process at an early stage and proactively reports them to the user in the chat room. This prevents excessive stress and unnecessary wear of components or line downtime in good time - completely autonomously, without the need for configuration. With a simple click on the machine notification, production managers receive all essential information on process parameters and key figures such as productivity, stability and order progress of all connected machines - if required, also of third-party machines. The time window selected for monitoring can be set to three cycles (1h, 8h, 24h).
Production monitoring
Messages about important events such as alarms or parameter changes during ongoing production are automatically sent by the machine in the form of a chronicle (machine messenger). Employees receive live push notifications on their desktop PC or smartphone and can subscribe to these as required for each machine. The intuitive structure of the "socialProduction" pages also allows quick access to important machine parameters. A complete log of all events, alarms and setpoint changes that have occurred on the machine control are additionally displayed in chronological order in a detailed view.
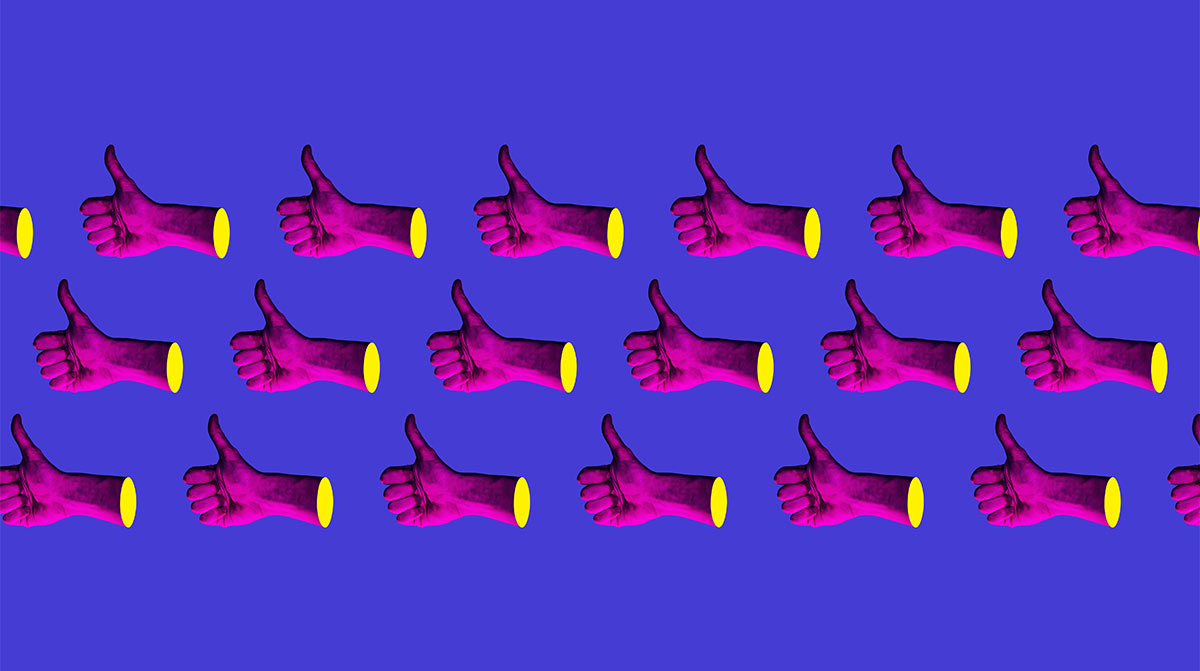
"Our machines learn with every like"
What makes machines "smart"? Dr. Christian Bartsch, Global Vice President Digital Solutions, KraussMaffei Technologies GmbH, gives examples from the application of "socialProduction".
DIALOG: Dr. Bartsch, at what point do people accept an injection molding machine as a teammate?
CB: As soon as support becomes noticeable. For example, shift handover: If I regulate this on paper and by Post-it, it is quite error-prone. However, the machine's tolerance rate for illegible writing or incomplete information is 0 - all information must be entered so that the next shift is optimally informed. Otherwise, the software "annoys" with inquiries or points out irregularities in the machine's chat room. If the process then quickly runs better, the human-machine interaction has become a bit more natural again.
Help with the right knowledge at the right time is also well received. No one wants to scroll through a page-long PDF or hear standard chatbot phrases when something goes wrong. Or when, as in the case of injection molding machines, 100 or more material and control parameters have to be finely tuned in the right combination to achieve top product quality. No one can keep track of all that anymore.
DIALOG: But couldn't a kind of injection molding Wikipedia be of sufficient help?
CB: No, lexical knowledge, even in digital form, is a collection of data that, depending on the quality of the search function, I sometimes have to slog through longer or shorter to find the right information. An application that proactively supports me, i.e. recognizes problems and directly suggests the appropriate solution options, is more effective.
Like our anomaly detection, which really "looks" at the process across all parameters and identifies outliers that can be insidious or erratic. However, since our plastics and process knowledge is now not only in the heads of the employees, but also in the self-learning algorithm of "socialProduction", this makes the work in production immensely easier.
DIALOG: And in the future, the machine will take care of everything itself?
CB: I don't think so, because with new customer requirements, the spectrum of what the machine has to do is always evolving. For the foreseeable future, we will need people to make these modifications: Product designers, engineers, data analysts. What is exciting about the further development are, for example, all the options with which we can further train the machines to analyze the enormous amounts of data and to communicate with us even more precisely and authentically despite this complexity.
Example: In the future, an employee at a customer site can simply respond to a message from the machine with a "like", in the sense of "fits, thanks". Then you know that the algorithm has done the right thing. They have already integrated another, very simple machine learning mechanism - and the machine learns with every Like.
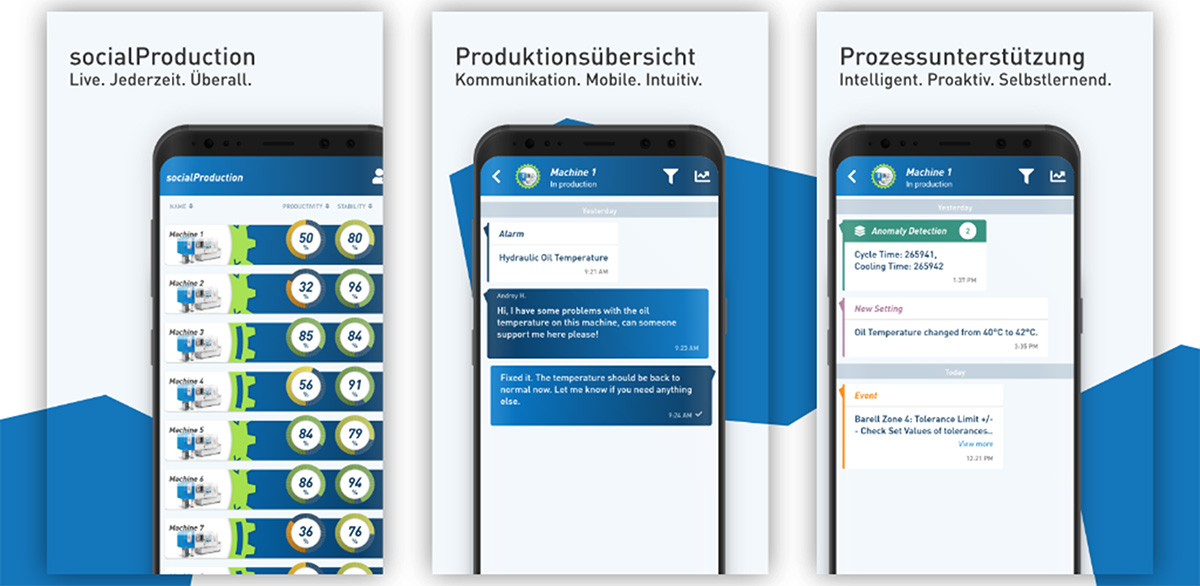
Field of application: Mechanical and plant engineering
Challenge
Increase attractiveness of digital manufacturing tools in human-machine communication; improve information flow on machine availability and scrap rate; reduce error rate in demanding injection molding process
Solution
"socialProduction", a mobile app and web application for injection molding machines that combines social media functions with technologies for production monitoring and process support; status information of the machines available live in secure chat rooms for employees; independent detection of deviations in the production process through AI/ML-based solution.