Digital shop floor management
Digital shop floor management in the Smart Factory is the further development of the classic concept of on-site management to control and stabilize shop floor processes in real time.
This is not about transferring analog shop floor management to a drive, visualizing key figures on a monitor or sending lists of measures via e-mail.
Rather, digital shop floor management is characterised by the following features:
- Collection of data relevant for shop floor management at its source and its automated use (e.g. MES / ERP systems, intelligent workflows)
- Visualization of real-time process and performance key figures through standardized calculation of source data
- Use of digital assistance systems such as machine learning for problem solving, which support the early identification of problems and causes of problems and the definition of countermeasures
- Structured knowledge storage and learning systems with standardized and cross-location knowledge distribution
These approaches make it possible to visualize relevant process and productivity data such as OEE, bottlenecks, cycle time deviations, process instabilities or quality problems in real time, thus creating the basis for fast and sustainable error or deviation correction (faster PDCA).
The automated and consistently designed connectivity of plants as well as a uniform data and information model has two decisive advantages. Firstly, cross-plant benchmarks can be carried out and secondly, administrative work can be eliminated through automation and freedom to solve problems can be gained.
Further fields of application of digital shop floor management are flexible shift and employee scheduling, reactive on-site resource control and fast reaction routines in the context of predictive quality or maintenance management.
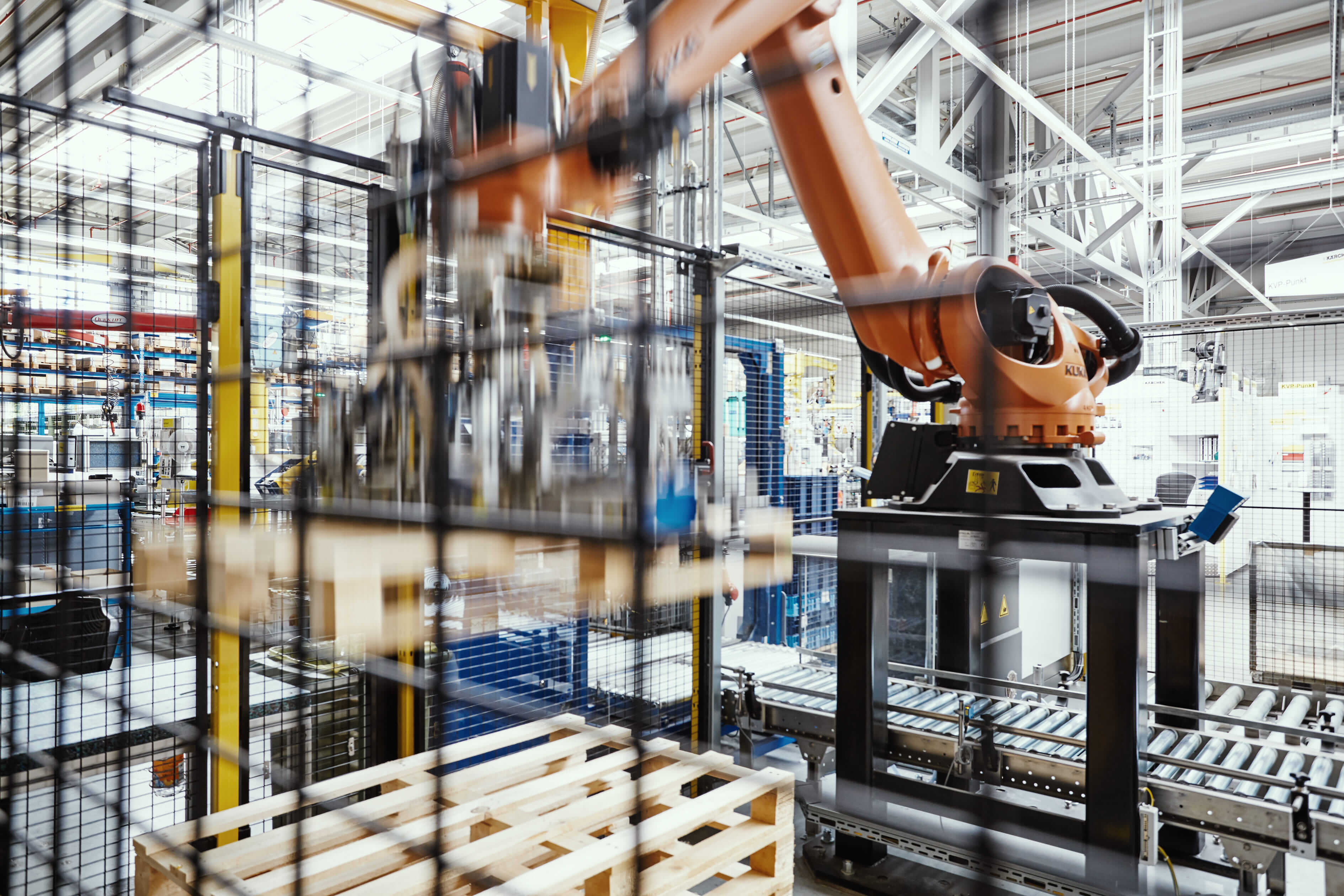

EFESO supports companies in the holistic planning and implementation of digital shop floor management from the conception to the anchoring of a culture of continuous improvement:
- Creation of a big picture of the SFM elements to be digitized, including a presentation of the influences on organization, qualification and management
- Derivation of the necessary IT modules and the functional/technical requirements, e.g. prerequisites for automated acquisition of operating and machine data (BDE / MDE), process parameters, measurement data
- Definition of the IT architecture and selection of IT tools, e.g. for visualization and analysis, data management and aggregation, hardware (SFM boards), system-based problem solving (e.g. EFESO Tool SOLVACE - www.solvace.com)
- Front-end setup: cross-location consolidation of data sources and user-oriented provision via shop floor boards and apps, ensuring defined standards and KPIs, real-time visualization
- Definition or upgrade of the analog SFM requirements
- Piloting and roll out
- Necessary training and qualification measures as well as accompanying coaching of the implementation.
DIGITAL SHOP FLOOR MANAGEMENT: THIS IS HOW YOU FIND THE RIGHT SOLUTION!
Digital shop floor management (DSFM) improves operational excellence, productivity, on-time delivery and quality and ensures better utilisation of production capacities. Smart tools that consolidate and distribute good practices, enable effective problem solving, help define and control KPIs, and support the initiation of learning processes play a central role.
A central prerequisite for the successful introduction of DSFM is therefore the choice of a software solution that fits the specific company requirements. However, solution providers focus differently on supporting one or more DSFM tasks, which makes the selection a challenging task.
The most important tasks of digital shopfloor management
- Can we document solutions to problems in such a way that we can use the knowledge in the next problem?
- Can we document solution-related data in such a way that it can be analysed and used for AI training?
- Can I assign tasks directly to a meeting and work as a moderator with an automatically created list of topics?
- Can I document the results of the meeting directly in the solution and access them later?
- Can I see all relevant KPIs for each Hoshin Kanri level in real time?
- Can I create reports myself, integrate machine data and calculate central KPIs such as OEE?
- Are problem-solving techniques such as A3 reports and Ishikawa analyses digitally supported?
- Can tasks be assigned to people or meetings and is status tracking possible through deadlines and milestones?
- Can ideas from the shop floor be quickly captured and evaluated?
- Can ideas be structured and distributed?
- Is the availability of employees possible, e.g. via calendar integration, and does it allow valid shift planning?
- Can the task-related qualification be mapped via a qualification matrix?
Top 5 requirements for a DSFM solution
- Process orientation
The concrete benefit of digitisation for the focused process is decisive. For example, a function for importing 3D CAD data from the plant can be useful. However, it does not create added value if the maintenance of the CAD data is not clearly regulated from an organisational point of view and is carried out with reasonable effort. Weigh up the costs and benefits function by function! to a DSFM solution - Modular software approach
Many companies have tools such as BI dashboards, SharePoint lists in use that are to be integrated into a DSFM solution. Make sure that the DSFM solution can be implemented modularly and can integrate existing solutions or connect them via API! - On-premise and cloud
Cloud-based solutions are increasingly standard. But many factories still struggle with Wi-Fi interference, unlit areas and latency. Consider a hybrid approach where key data is local but factory comparisons are enabled by historical data in the cloud! - Self-service and customising
The requirements for meeting structures and design are dynamic and vary from plant to plant. The quick and uncomplicated change of content is therefore crucial for productivity and cost efficiency. Make sure that customising is comprehensively possible! - Runability on mobile devices
A future-proof DSFM solution must continue to be optimised for desktop use. However, it must support mobile devices and the corresponding processes - for example, to enable fast and flexible documentation of machine damage and immediate assignment of work orders. Check whether mobile use is possible without restrictions!
DSFM providers: Structure of the market
The market for DSFM solutions is confusing. Specialists who cover individual elements, MES experts who offer DSFM functionalities as add-ons, full DSFM providers, or platform operators who provide tools for developing their own solutions compete with each other. The following overview shows some high-profile players.
Against this background, the selection of the appropriate solution is not exclusively a question of technology and functionality, but requires a holistic, company-specific consideration. The following aspects need to be considered in particular.
Four recommendations for selecting a DSFM solution
- Review of the SFM in practice: Putting the SFM routines in practice to the test and improving them is the first step towards defining and weighting the requirements. The agile approach, in which the end users communicate their needs directly via user stories, has proven successful in this context.
- Benefit-oriented function selection: There is hardly a function for SFM that is not technically solvable. But which functions and modules really offer added value? Whether the live visualisation of key figures or knowledge management in dealing with deviations is particularly valuable must be decided on a company-specific basis.
- IT landscape: If the implementation is to succeed, the DSFM solution must fit into the IT strategy and architecture. It must also be defined which applications that exist today are to be retained or replaced and which scope of possibilities for in-house development is currently and prospectively sensible. Close involvement of the IT department is critical to success.
- Take changed competence requirements into account: Intuitive DSFM solutions also require staff to change their usual working methods. Therefore, it is advisable to start in areas with a higher affinity to IT and to react early to identified training needs. Sustainable success of DSFM depends on broad acceptance.