Shop floor management
The central management instrument in the context of Lean Production, Smart Factory and Industry 4.0 is shop floor management.
While Lean, OPEX and digitization initiatives generally focus on the implementation of process-related and technical improvements on site, shop floor management focuses on the operational control and short-cycle stabilization of value-adding processes: through clear structures and target systems, stringent process organization and work standards across all hierarchical levels.
The starting point is a cascade of key figures that enables clear and coordinated targets to be set for the areas involved in shop floor management.
Divisional targets are supplemented by operating result and process key figures, which form the basis for local control. By means of this key figure system, target-performance deviations are clearly and transparently recorded and measured at every level in order to be able to initiate targeted and rapid stabilisation and improvement measures (KATA).
Effective and efficient shop floor management is characterized by the following elements:
- On-site management
Managers live the mentor-mentee dialogue and empower their employees in problem solving. SFM meetings and problem solving take place on site. Roles and responsibilities are defined and lived at all levels. Representation and escalation are clearly regulated
- Working with targets
Goals in your own area of responsibility are derived from higher-level goals, converted into SFM-compatible process key figures that can be influenced on site and pursued by means of target/actual comparison. The key figures are collected and reported by the employees on their own responsibility in a cyclical and reproducible manner.
- Working with standards
Both work equipment and methods on site and routines for problem solving are standardized and uniformly structured. Defined SFM time windows are firmly scheduled across all levels of the hierarchy and are adhered to by all those involved.
- Visualization
The SFM boards are used to visualize and track key figures, their deviation from target and actual values, and the degree to which defined measures, including responsibilities, have been processed. The contents of the SFM tables are uniformly structured, up-to-date and comply with the specifications. In the meantime, it has proven to be a good idea to start with digital shop floor management systems immediately, as these can be introduced quickly and the transparency of the information can be improved considerably. EFESO has an excellent overview of the systems available on the market and their specific advantages and disadvantages.
- Communication
A hierarchical information cascade is defined, the team leader and foreman level is included. For the information cascade (regular communication) time frame, contents, duration ("script") and necessary participants are defined.
- Qualification
A qualification plan for managers on the basics and principles of SFM exists and has been implemented. Managers and responsible persons are trained in such a way that daily problem solving on site is possible. If additional support is required, communication channels are clearly clarified.
Shop floor management approaches have not only proven themselves in production, but can also be successfully implemented in indirect areas such as logistics, quality or maintenance as well as in administrative functions, but also in project business.
Shop floor management always also serves as a yardstick for the implementation success of the Kaizen philosophy of continuous improvement. Recurring and small-scale problems on the shop floor as well as long "open points lists" are proof that not the actual causes of the problem, but often only the symptoms are eliminated.
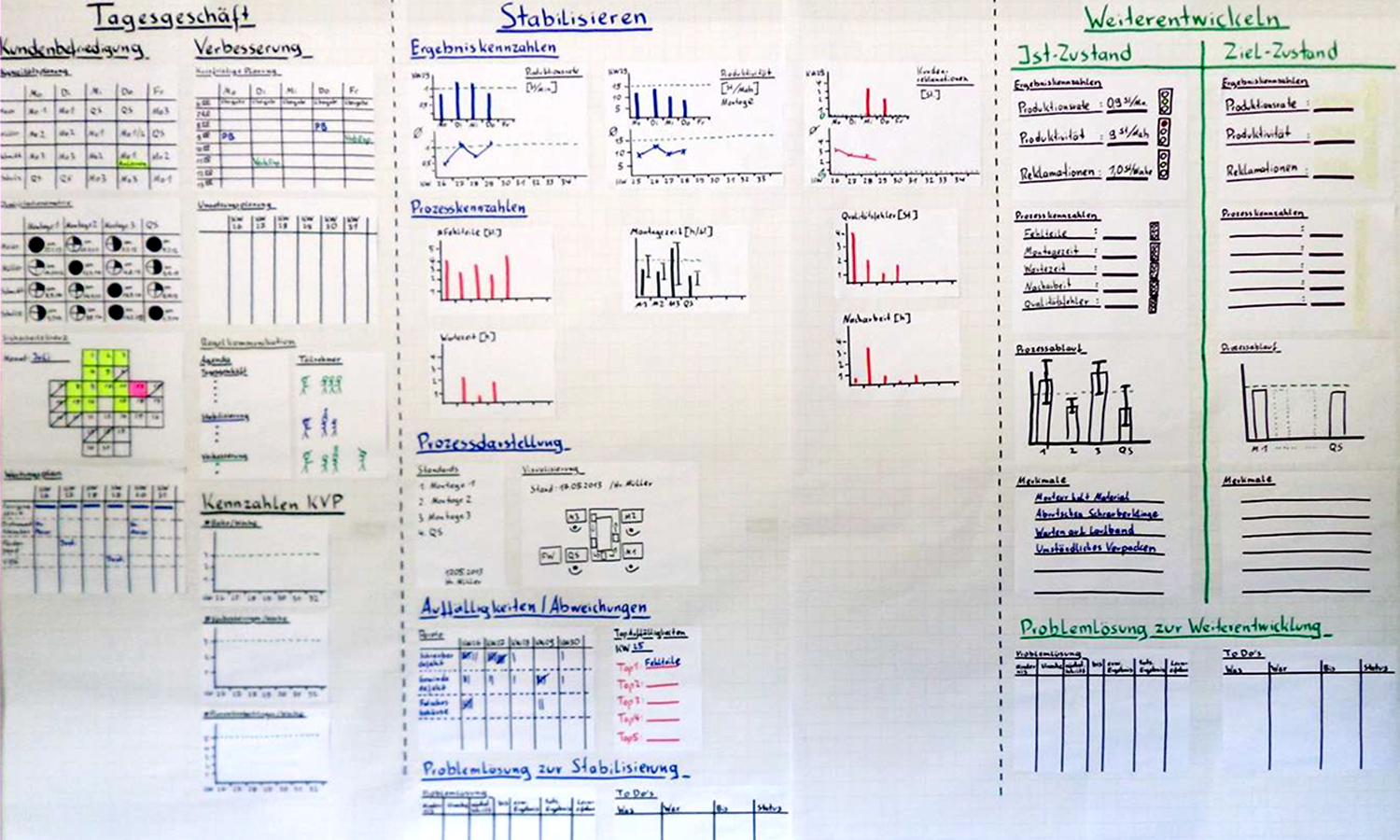
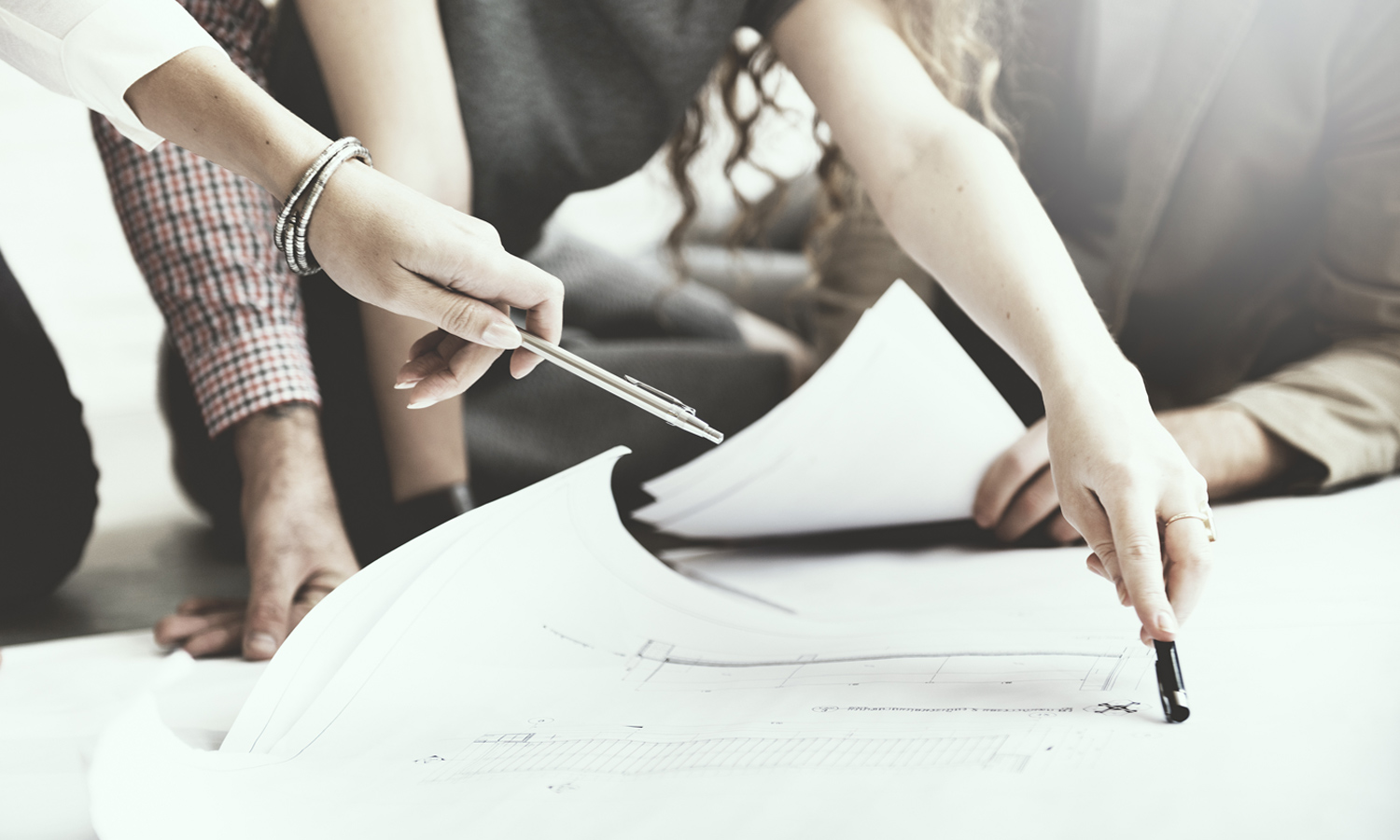
EFESO supports companies on their way to a culture of continuous improvement by a practice-oriented introduction or further development of shop floor management.
We offer the following services:
- Maturity level analysis / SFM scan
Using a quick and structured shop floor management scan, we evaluate the current status of implementation, point out the gaps to best practices and define specific action points and qualification requirements
- Pilot introduction
A pilot implementation creates acceptance and understanding for the methods and tools of an effective SFM and serves to test or further develop principles and best practices that have not yet been implemented
- Roadmap and Rollout
Based on the pilot experience, the roll-out is organised in the factory or group of factories or the further development towards digital shop floor management using industry 4.0 technologies is planned
- Training and qualification, coaching
In addition to setting up the necessary structures on site, managers at all levels are prepared for their roles and responsibilities in practice-oriented and didactically sound training and qualification programs. Active and practical coaching based on the train-the-trainer approach supports successful implementation.