In the project setup, EFESO collects all necessary information and thus creates the basis for all subsequent steps of product industrialization. This includes, in particular, know-how about the existing product development process and about known gaps. Also important is information about the organization, project management and the characteristics of the IT infrastructure.
Product Industrialization & Ramp-up Management
In the context of a product engineering process (PEP), "industrialization" refers to the phase of transferring a product from development to series production. In this phase, companies integrate a product or a product idea into their manufacturing line(s).
This includes different tasks. In addition to optimizing the product design for mass fabrication, suitable machinery and equipment must be selected. Furthermore, manufacturing guidelines and quality standards have to be developed and employees have to be qualified. Reducing production costs, shortening lead times and ensuring consistent product quality are the classic objectives of product industrialization.
However, in PDP practice, this important issue is often not adequately addressed. This is reflected, for example, in poorly designed interfaces between the project and series organization and between plant locations. In the worst-case scenario, this leads to delayed series start-ups, unnecessary scrap and additional costs, e.g. due to unplanned extra efforts (task forces) or special trips. The economic viability of the product can therefore be jeopardized right at the beginning of the product life cycle.
Closing gaps in the PDP
To solve the challenges of product industrialization - including product ramp-up / ramp-down - EFESO combines the following measures in a approach specifically tailored to this topic:
- Using a detailed catalog of questions, we identify and quantify the gaps in the PDP in two dimensions (basis: 250 questions): first, what is the maturity level of current product industrialization? Secondly, what is the actual reality lived out in day-to-day work?
- This shows the concrete need for action in the PDP, since deviations from best practice standards can thus be measured. The subsequent application of the questionnaire shows the progress made. In addition, we thus avoid inefficient "brainstorming workshops". Instead of subjective opinions, the main purpose of this approach is to exchange factual knowledge in order to derive the best possible PEP.
- Based on this, we close the identified gaps and use best practice experiences for a targeted and time-saving process (e.g. 3P workshops, APQP). By conducting "Change Readiness Assessments", we take into account the employees' readiness for change from the very beginning and develop customized roll-out guidelines for change management and employee qualification.
Solution paths according to customer needs
Our approach is based on the experience and results of customer projects, is continuously developed by us and adapted in product industrialization projects according to the company's situation and objectives. Our clients benefit from a structured and efficient approach in the following project phases.
Product industrialization: approach of EFESO
Identify baseline
Determine status quo
We use our 250-question questionnaire to identify gaps and weaknesses in the PDP on a cross-functional basis. We take two dimensions into account: the current degree of implementation and the "lived" maturity. After all, the fact that a process has been described and trained does not automatically mean that it is also being applied, communicated and improved.
Define processes and trainings
In the course of a "Change Readiness Assessment", the project team records the organization's readiness for change. In cross-functional workshops, we now close the identified gaps, primarily via these measures:
- definition & presentation of new and existing process steps in the PDP
- process description (input, task description, output, participants, tools, templates, etc.)
- definition of the RACI matrix of the processes
- comparison of the degree of implementation of closed gaps in the PDP via best-practice blueprint questionnaire
- determination of the necessary training, transformation concept and requirements on the process side; creation of corresponding documents and IT requirements, e.g. workflows, etc.
Introduce process and coach employees
In the implementation phase, we focus on PDP training and change management. This includes a clear definition of a master plan for the change steps as well as for monitoring results. All activities here take into account the levels of factual change (e.g. defining and anchoring new processes and responsibilities) and mental change (e.g. continuous monitoring and support of the entire change process).
Success factors: mastering product ramp-up
- Describe processes and standards in detail and at the same time in a comprehensible way
- Establish and develop cross-functional teams and local ramp-up managers
- Identify and establish effective controlling, reporting and steering instruments
- Intensify risk management, e.g. promote proactive identification of late changes
- Ensure management attention, e.g. with regard to process compliance, prioritization, escalation
- Realize a transparent end-to-end value stream, involving suppliers and (end) customers
Success factors: Implement a new PDP
- Design the PDP simply, clearly, unambiguously and completely together in the cross-functional team
- Ensure the traceability and accessibility of the PDP. This requires, among other things, that the responsible employees must be proficient in the relevant IT tools (software)
- Enable or encourage employees to identify with the process in their roles and responsibilities
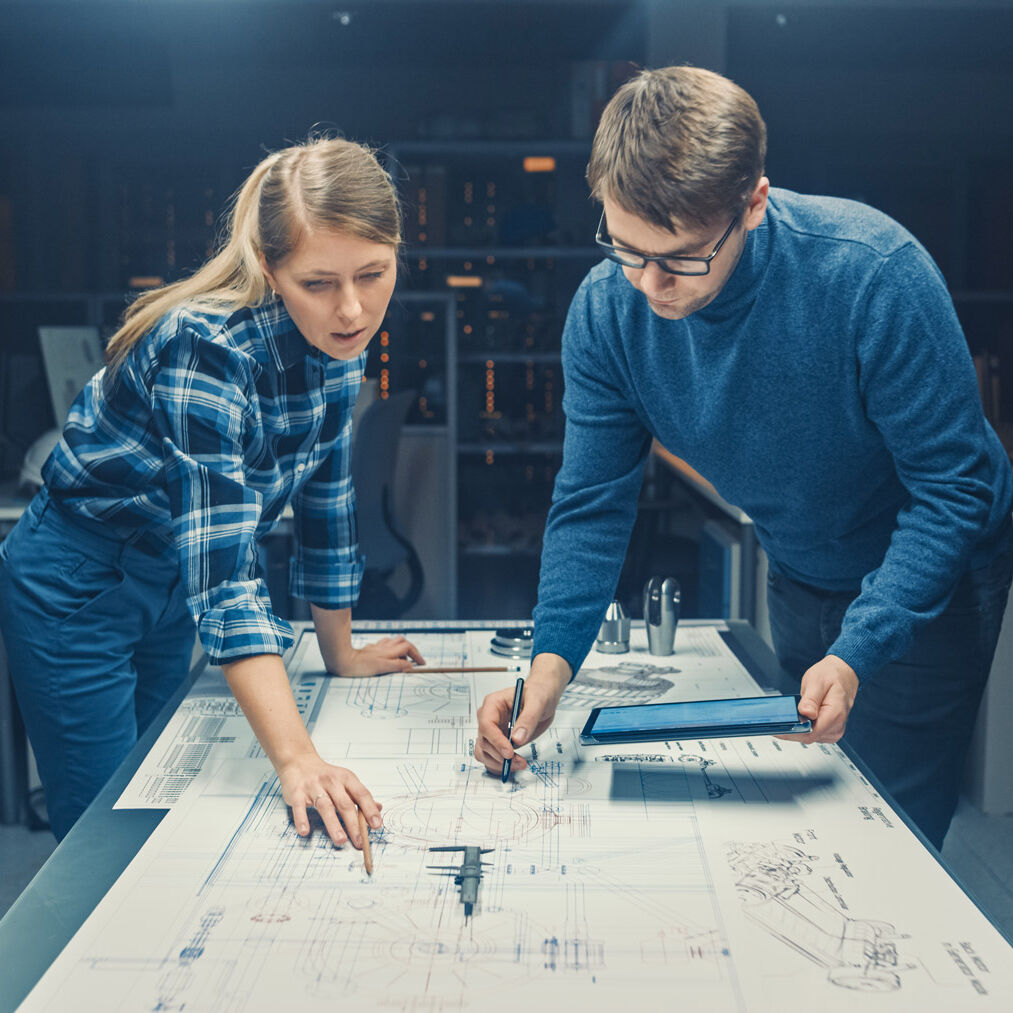
Project: Design and implementation of a robust, efficient and standardized PDP including product industrialization and ramp-up management at a Tier 1 supplier (approx. 10,000 employees worldwide).
Results:
- Complete elimination of gaps in the existing PDP after one year, especially with regard to product industrialization.
- Worldwide rollout of the new PDP incl. implementation / employee training.
- Plants are involved in the PDP and take over at an early stage through local ramp-up managers and sub-project managers with industrialization responsibility.
MORE SERVICES