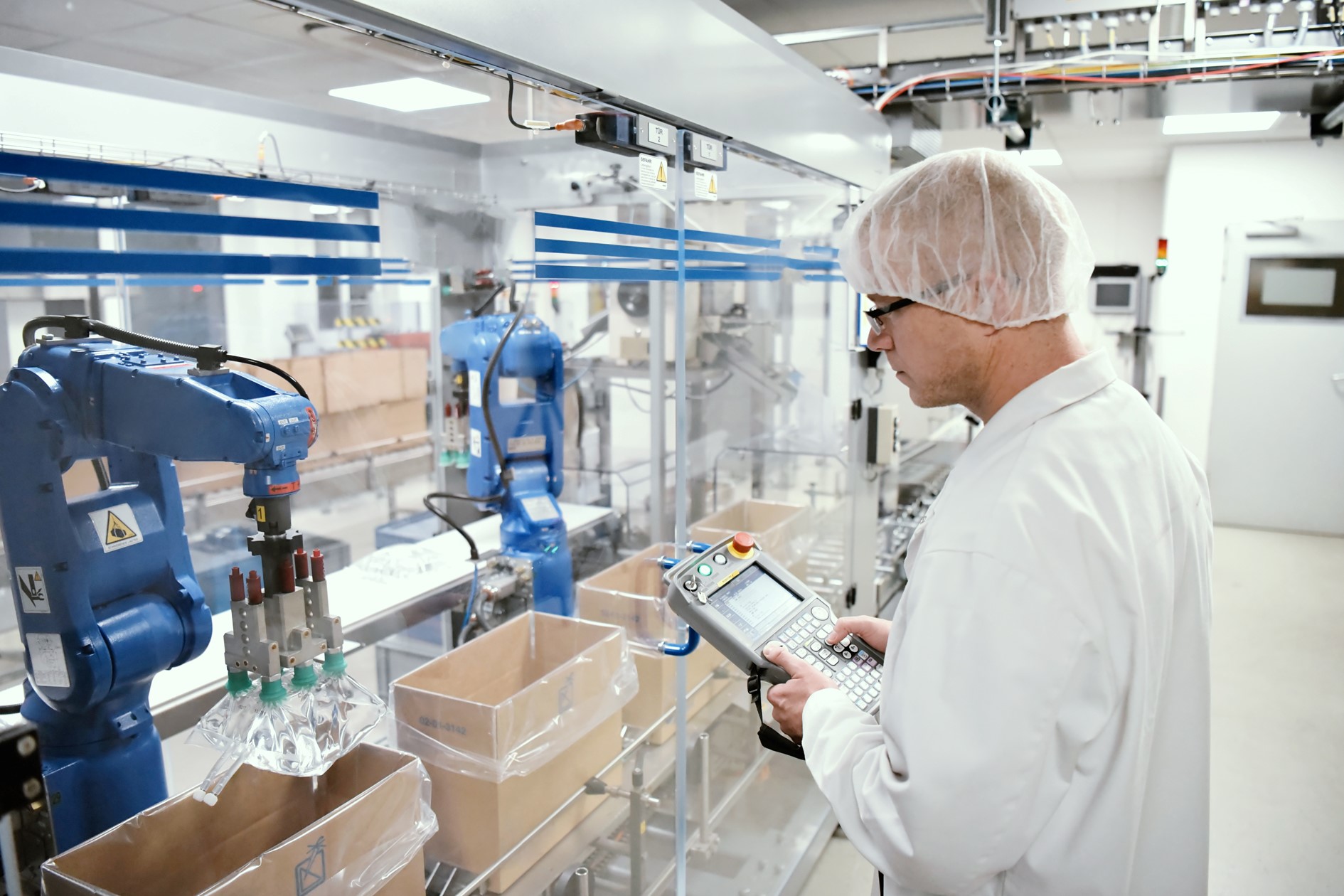
Target image for the transformation to the Smart Factory
End-to-end supply chain digitalisation in the healthcare sector
Putting together and ordering the desired product according to your own needs at the click of a mouse in the online configurator: these customer requirements must not only be met by companies in the consumer goods industry. This interaction is also highly relevant for manufacturers of medical, customisable products. However, whether assistants, support stockings or other products expand the B2C business in this way depends on the digital maturity of the logistics and production processes. This is exactly the situation faced by a leading international manufacturer and supplier of medical and hygiene products. In order to strengthen its rapidly growing B2C segment and develop data-based service and business models, the company wanted to develop its supply chain in line with customer and market requirements. Together with EFESO, it created a new, fully digitalised end-to-end supply chain.
Challenge
A leading international manufacturer of medical and hygiene products wants to redesign its supply chain and digitalise it throughout. The aim: to strengthen the growing B2C business and support new, data-driven service models. With EFESO, the company is implementing a project for end-to-end digitisation.
MOREEFESO approach
Development of a holistic approach from two perspectives: top down and bottom up, to ensure a broad consensus for the Industry 4.0 transformation process at an early stage. Appointment of cross-location topic leaders and establishment of "centres of excellence" for digitisation in the various topic areas.
MORELessons learned
In order to sustainably use the digitalisation of the supply chain for new service and business models, customer service must be improved and employees must be supported by digital support solutions. Apps, assistance systems and the digital workplace are essential for this process in the Smart Factory.
MOREEFESO success model
EFESO's I4.0 Scan enabled all relevant processes for the end-to-end digitalisation of the supply chain to be identified and the appropriate IT architecture to be implemented and further developed to be future-proof. The focus was on customer orientation and Operational Excellence 4.0.
MOREFarewell to the standard product
In the future, medical products will not only provide information about the user when they are used, but also already during their development. Whether contact lenses, medicines or surgical instruments - everything that can be adapted by the user for the user or patient has potential. However, it is not only the product properties that often prove to be the complexity driver. The spectrum of technologies that enable the production and distribution of personalised products is just as difficult to grasp: web configurators, video scans, health apps, production machines, track & trace software for logistics and many other stations must be correctly selected and coordinated.
The challenge for EFESO in this project was to define the right mix of Industry 4.0 building blocks and technologies for the digitalisation of the supply chain across different company locations. This also had to be brought into line with the respective customer and market requirements. In only 12 weeks the project team managed to implement all project steps from assessment, I4.0 strategy and a "target picture" to the roadmap and to start the implementation. The combination of best practice experience, process know-how and digital competence that EFESO brought to the project ensured acceleration and time savings.
The implementation started just 12 weeks after the project started.
Status Quo and I4.0 Scan
In the first phase of the project, the EFESO team first determined the status quo at the production sites using assessments and diagnostic tools: What does the respective production and logistics process look like? To what extent has the value stream in the plants already been digitalised? Are there certification specifications or regulatory requirements in the countries that need to be taken into account?
To answer these and other questions and to evaluate the maturity level of the organisation in the plants in a structured way, the company uses the I4.0 Scan developed by EFESO. This focuses on two approaches or perspectives: firstly, "top down" to include the corporate strategy. On the other hand "Bottom Up", i.e. an analysis of the processes, systems & organisation to determine their potential.
Top Down and Bottom Up
At the top down level, the team discussed with management the strategic requirements that would change the organisation, leadership and corporate culture when moving towards I4.0 and Operational Excellence (OPEX 4.0). At the bottom-up level, it first determined the country-specific market and customer requirements of the locations with interdisciplinary teams from production, SCM and quality management and analysed the respective digital maturity level.
Using the I4.0 scan, all relevant processes for the end-to-end digitalisation of the supply chain in the areas of scheduling, production, logistics, quality, controlling and maintenance could be recorded and the existing IT architecture examined. In this way, the scan ensured transparency and enabled the project team to evaluate the initial situation in a structured way, collect ideas and derive options for improvement.
Fields of Action on the way to the Smart Factory
The second phase of the project was to develop a common understanding of where the company's I4.0 journey should take it. In this way, the project team not only formulated an Industry 4.0 vision, but also identified the concrete goals and key areas for action to make this vision a reality. The pragmatic approach followed by the project team was based on a uniform and consistent "end-to-end" process: from customer requirements to individual customisation and the delivered product. The technologies and services required for this were to make the digital value-added chain and thus the entire SCM process future-proof. An important goal was to use "Digital Workplaces" to develop the locations into "Smart Factories".
The company uses the Industry 4.0 Scan to assess the digital maturity of its processes and organisation.
Target Picture for Operations & SCM
On the basis of the knowledge gained, EFESO has now developed a joint "I4.0 Target Picture" with the location teams and management. While the management level dealt in the workshops with the organisational concept for the implementation of the digitisation measures and the necessary investments, the production and SCM teams concentrated on the large, common I4.0 target picture for all production sites. This was an important point, because often when planning the Smart Factory, there are different ideas regarding technologies or organisational forms for these upcoming transformation processes. The common "target picture" clarifies where the journey is to go, how the implementation can function in concrete terms, which solution modules are necessary for this and what potential benefits this will bring to the organisation.
The Target Picture clarifies the destination and provides the necessary transparency for all parties involved.
Digital value stream and seamless customer and supplier integration
In order to implement the company's goals - strengthening the growing B2C sector and supporting new, data-based service and business models - the new I4.0 architecture had to be future-proof above all. To this end, the project team defined three key criteria:
- A digitalised end-to-end supply chain, which allows the company to react to changes in customers or the market at any time.
- A digital value stream that guarantees real-time monitoring of all movements, inventories, product, process, quality and performance data along the entire value chain.
- A seamless customer and supplier integration from the digital order, the "make-to-measure process" or individual product configuration to "track and trace" options for the customer. In particular, the simple and fast integration of the company's service providers and partners was crucial in order to increase delivery capability and reduce delivery times.
Once the customer has configured his medical product, the order is placed at the push of a button and the process runs automatically along the value chain. Product individualisation through the "Configure-to-Order" process via a web configurator leads to more variants and smaller batch sizes. In order to ensure resource availability, EFESO merged the MES and ERP systems of the company's various brands in such a way that all data of the manufacturing and logistics processes are available in real time.
Centre of Excellence
In order to ensure that those involved in the process at the sites implement the transformation processes for end-to-end digitisation independently, EFESO set up competence centres to drive the process as responsible parties. For these "centres of excellence", cross-location topic managers were appointed and qualified within the framework of the implementation projects.
Results: Effective use of digital tools
The results since the beginning of the implementation phase are clear improvements in ...
- the ability to react to customers due to a continuous flow of information;
- increased delivery performance and delivery times;
- cost-optimised processes and an increase in productivity through optimised plant support and management;
- quality assurance through automatic recording and analysis of quality parameters.
Digital solutions such as apps, intelligent assistance systems or 3D work instructions are also used to support employees in the operational and administrative areas.
Guarantees for implementation: Centre of Excellence and cross-location topic managers.