(Kopie 1)
The deserted warehouse
By Dr. Wolfgang Keplinger, ROI Management Consulting AG
Warehouses and distribution centres of the future are more efficient, more reliable, faster, smarter - and, above all, deserted. Because robots are now so cheap and energy efficient that they have almost completely displaced the people there. What‘s more, they change the way people work there. The number of work steps is no longer key for the efficiency of a process - the operating costs of the individual robot is. The almost unlimited availability of robotic work is thus used to leverage huge efficiency gains and forever changes the look of the warehouses:
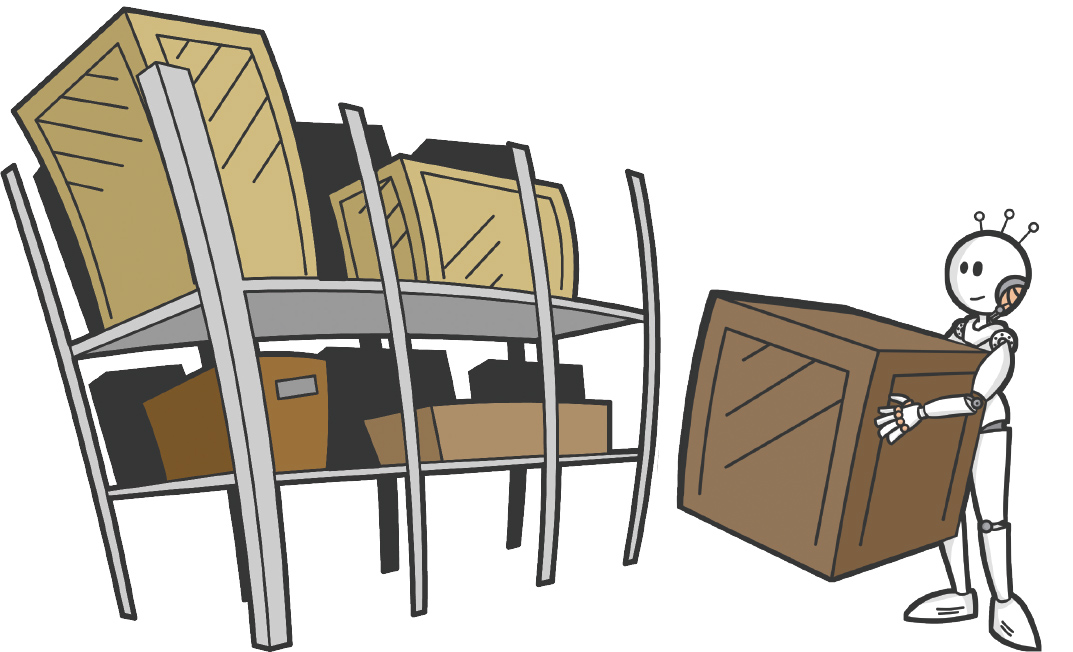
Dynamic localization
Warehouse 4.0 will know dynamically, in real time, where the materials/articles are currently located - whether in intake or already on the way to the customer. The use of RFID and beacons then allows us to use Smart Boxes, Smart Bins and Smart Racks, with which any material can be localized at any time. If the products themselves become smarter, we no longer even need the support of “logistics RFIDs” because at that point the scanners in the warehouse will communicate directly with the smart products. With further development of known localization technologies (e.g. DGPS or UWB), methods such as geofencing will also be used within the warehouse in the future.
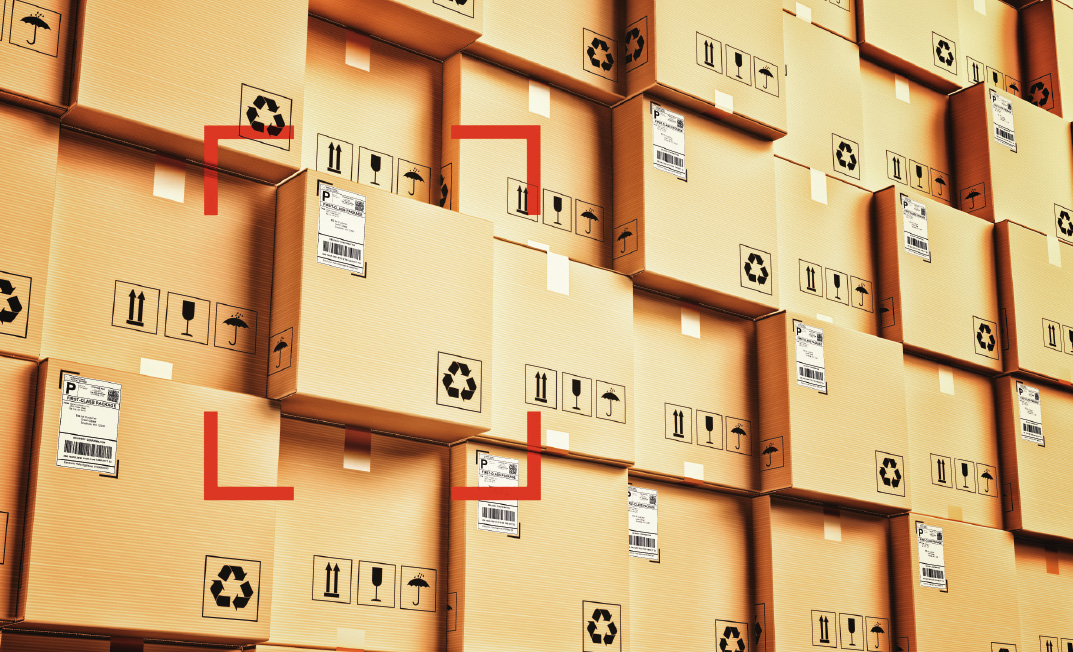
Automation through Cobots and Picking Robots
Warehouse automation geared towards efficient goods-to-man systems has made considerable progress in recent years thanks to the development of shuttles. Their advantage: they are scalable, with one shuttle per level and aisle, they allow for higher storage/retrieval performance than a storage/retrieval unit (SRU) and are relatively insensitive if a shuttle ever fails. Since the moved masses are significantly lower than those of SRUs, the energy balance of a shuttle system is better than that of an SRU, an important argument in favour of green logistics.
The almost unlimited availability of robotic work is thus used to leverage huge efficiency gains and forever changes the look of the warehouses.
Automatically Moved Racks
Amazon creates efficient nesting order picking with fully automatic robots that bring a whole shelf rack auto-propelled to the picking station by driving under the shelf and lifting it. The benefits for Amazon: The lack of travel time yields a 50% to 70% increase in efficiency for the company. Further advantages are the increase in storage density (articles stored per unit area), scalability of the system, insensitivity in case of failure of a robot, and low energy consumption. Besides robot manufacturer Kiva, which has been acquired by Amazon, Swisslog also offers a similar, highly efficient system for e-commerce providers or mail order companies with its Carry Picker.
Short market cycles and volatile demands are forcing companies and logistics service providers to design their warehouse hardware in a standardized, scalable and flexible manner in the future.
Cellular/Collective Intelligence Shuttles
Transporting within the warehouse, from the warehouse to the dispatch area or from the warehouse to production or back again are handled more and more by AGVs (Automated Guided Vehicles). In recent years, the vehicles have become smaller, more reliable, more autonomous in their control, more cost-effective and safer, and above all, independent of firmly laid out route guidance means such as cables, lines or markings. The vehicles control themselves more and more reliably through laser scanning and alignment to permanently installed orientation marks or by means of camera-based environmental/contour recognition.
While handling or transfer processes between the warehouse shuttles and the AGVs for further transport are still necessary today, in the future the shuttles could also travel to the shelf apron area and deliver the desired material directly to the picking station or into production. This eliminates yet another touch from the intra-logistics chain and brings us closer to a „no-/few-touch“ warehouse. The first attempts at a collective intelligence-based shuttle system that delivers directly from the shelf to order picking stations or production took place several years ago by the Fraunhofer Institute and Dematic, which made technological differences between racking and autonomous ground operations; but this solution is not yet economical.
Drones in the Warehouse
Drones performing the inventory in the warehouse no longer surprise anyone today. But where drones fly through the warehouse today and activate the RFID transponders of the stored products with an RFID reader, no drones will be heard in the future. Dynamic localization will make these deployments redundant. However, drones have a great future as a means of transport: In Warehouse 4.0, they will provide fast and direct exception express transport within a building, or even on short-haul routes. In this case, a drone could provide the much needed last link in a logistics chain to complete as extensive customer supply or start a production. Also conceivable is the use of drones in a clearly space-limited and outlined storage area, for example, to perform sorting tasks (from a track in KLTs or on pallets).
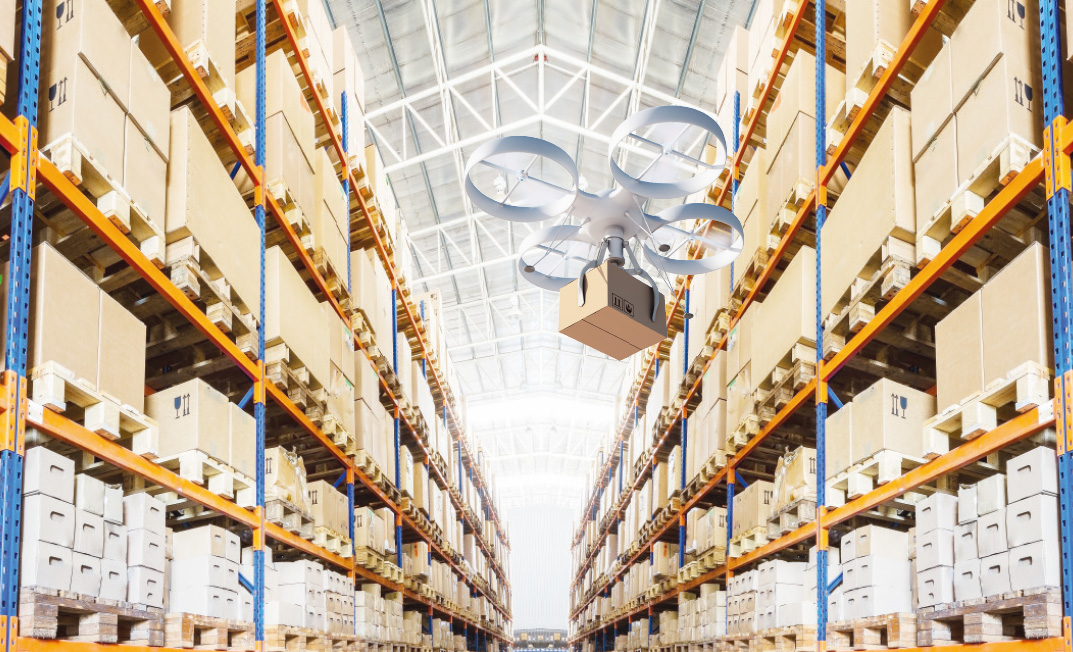
Hubs2Move & Virtualization of Warehouses
Short market cycles and volatile demands are forcing companies and logistics service providers to design their warehouse hardware in a standardized, scalable and flexible manner in the future. This is the only way warehouses can be adapted to the changing needs of customers. The next steps in this direction will then be to make the warehouses more portable (transfer from location A to location B) and more virtual. In this case, the physical transport of products could be largely replaced by a „transport of information“ over the internet. The customer then creates the final products himself by means of additive manufacturing/3D printing at the place of need.
The best warehouse is not a warehouse. The „advanced technologies“ are working to fine-tune the last bas-tions of stacking and layering. Through a mix of LEAN methods, digitalization, automation, mobilization and flexibilisation, the traditional warehouse not only loses its importance, but also more and more any physical substance. The notorious last one to switch off the light will certainly not be human. And therefore probably did not need the light on to begin with.