INDUSTRY 4.0 PREMISES FOR THE SMART FACTORY
How bonnets, doors, tailgates and vehicle roofs are manufactured with future-oriented Industry 4.0 technologies can be experienced in action on the outskirts of Halle (Saale) since the summer of 2021. In about two years, a press shop for the production of car body parts was built there on a greenfield site. As a joint venture between Porsche and Schuler AG, the "Smart Press Shop" plant combines the expertise of a car manufacturer and press builder in order to jointly develop and realize new products. In doing so, Smart Press Shop acts as a neutral supplier on the market; all plant parameters are compatible with Daimler, BMW, and the VW Group.
A highlight of the plant is the fully autonomous set-up process for the provision of press tools, which enables competitive production of small batches. Closed cycles and operation with renewable energies also minimize CO2 emissions in the production of the outer skin components made of aluminum or steel. The number of suppliers of such components has been declining for some years, while at the same time the demands on product quality have been increasing. Against this background, the idea of implementing the smart and fully networked press shop based on Industry 4.0 technologies was born.
Automation increases efficiency
The plant is equipped with a forward-looking, vertically and horizontally integrated IT infrastructure to create the highest possible level of connectivity at all levels between machines and workers. But the project's objective encompasses much more than that, with seven Industry 4.0 premises:
- Vertically and horizontally integrated IT infrastructure: Right from the start, data silos are to be avoided and the data flow is to be guaranteed despite the highest IT security. All machines and systems are connected via PLCs and networked in the cloud.
- Automated, self-optimizing processes: This not only involves purely physical processes, but also automated order and feedback processes, (self-)optimizing straightening aids and camera-based process monitoring.
- 100 percent paperless processes in production and administration
- Digital documentation: This includes, among other things, the topic of worker management. For the purpose of transparency and process optimization, manual processes are also reported back digitally.
- Real-time data available everywhere and at any time: All information generated by the plants can be viewed and analyzed at any time and anywhere.
- Resource-saving production through closed loops (Close Group Material), e.g. recycling of pure aluminium in a closed loop.
- Digital product and process twin: All generated machine, operator, product and process data are stored at product level and are traceable for the customer. This is also used for big data analytics
Already in the start-up phase of production, it became apparent that this approach works in practice and brings significant results. For example, due to a fully autonomous set-up process during press tool provision, the production team sets up the press line at least 50-70% faster than any other press shop. This enables competitive production of small batches.
Two heavy-duty cranes, each weighing 65 tons, play a central role here. These can load the press line equipment with the correct tools in parallel and fully automatically, depending on the incoming production orders. Not only is the tool store managed fully automatically, but the tools are also deposited automatically using optical safety technology. The pressing tools, which weigh several tons, are transported on and off by an autonomous tool crane, clamped automatically and media are docked automatically. In this way, the total setup time for the machine, including loading and distancing, is only three minutes. The time for production preparation, i.e. for transporting six molds to and from the line, can be halved or even tripled compared to a conventional press shop.
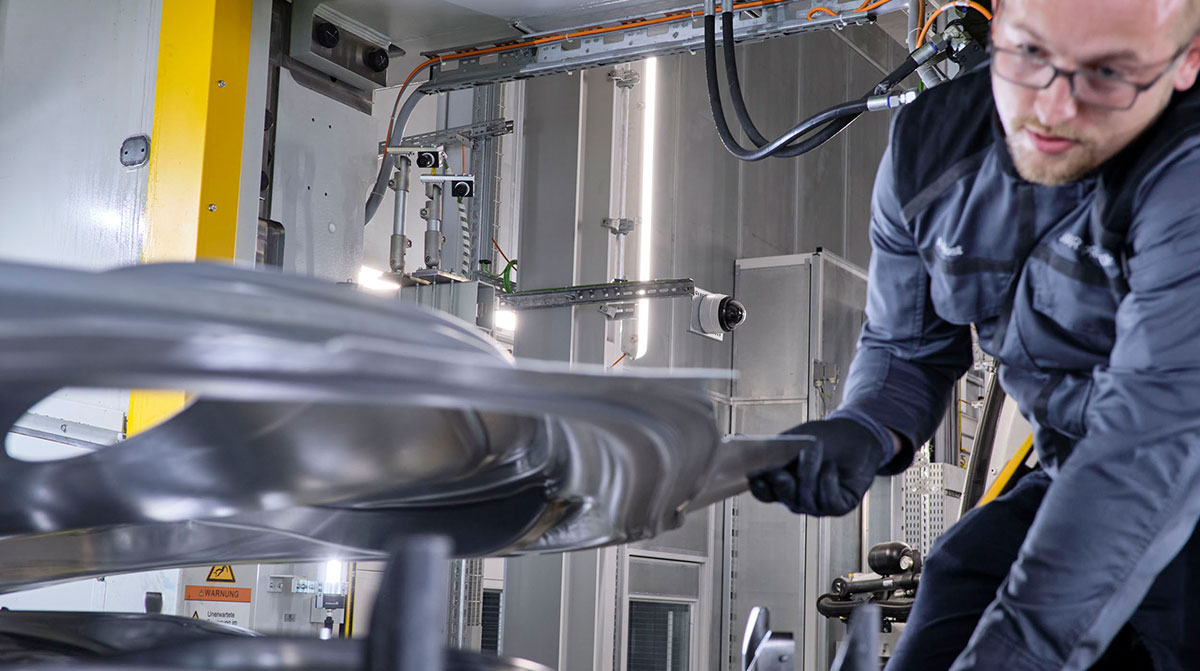
Increased productivity with reduced resource consumption
As a first mover, the Smart Press Shop project team had to overcome classic Industrie 4.0 challenges, such as compensating for a lack of standards in areas like IT security or digital documentation with its own solutions. In the process, major benefits have already been achieved: All workers as well as all machines and plants are networked via the cloud and all processes provide real-time data that can be viewed anytime and anywhere. This means that every part produced can be tracked from start to finish. However, positive results do not come "automatically" just from the availability of new technological tools. Ensuring the acceptance of these tools by the employees proved to be a decisive component and success factor of the project.
The key performance indicators of the Smart Factory speak for themselves: With an acceleration of the machining processes, the lead times can be reduced by a quarter. Set-up times alone are reduced by around 60 % thanks to fully autonomous set-up. This means that batch sizes that can be 60 % smaller are also possible, as well as 30 to 60 % lower inventories.
But of course, even a highly digitized smart factory is never completely mature. In the future, production planning will be supported to a large extent by AI. Currently, planning is mainly done manually in order to train staff on the processes. In addition, employees will increasingly use mobile devices such as smartwatches in the coming years.
Another further development concerns quality management. Here, an optical quality control is planned that will enable fully automated defect detection and component-related defect analysis of finished parts based on cameras and with AI support. This makes deviations from the specified degree of perfection visible quickly and reliably and allows a closed quality control loop for the smart factory.
Field of application: Automotive industry
Challenge
New construction of a smart factory with state-of-the-art IT infrastructure; high level of networking of machines and workers at all levels, 100 percent paperless production and high productivity with low consumption of resources as the most important objectives for the operation of the plant.
Solution
Implementation of seven Industry 4.0 premises with a vertically and horizontally integrated IT infrastructure as the central element; all machines and plants connected via Programmable Logic Controller (PLC); processing of time-sensitive information and commands via Programmable Logic Controller (PLC) and Supervisory Control and Data Acquisition (SCADA); all systems from MES level hosted in the cloud.