BEST PRACTICES OF INDUSTRY 4.0
SMART VALUE-ADDED ASSISTANTS
Even with a high level of automation in manufacturing, there is still room for improvement - for example, with cross-departmental process automation. In this case, EFESO used tools based on Robotic Process Automation (RPA) in the Operations department to save time and reduce the workload of employees. The smart helpers already passed the practical test in the first project phase: After only three months, the RPA tools were already handling 14 processes in eight business areas such as R&D, HR, controlling and quality management.
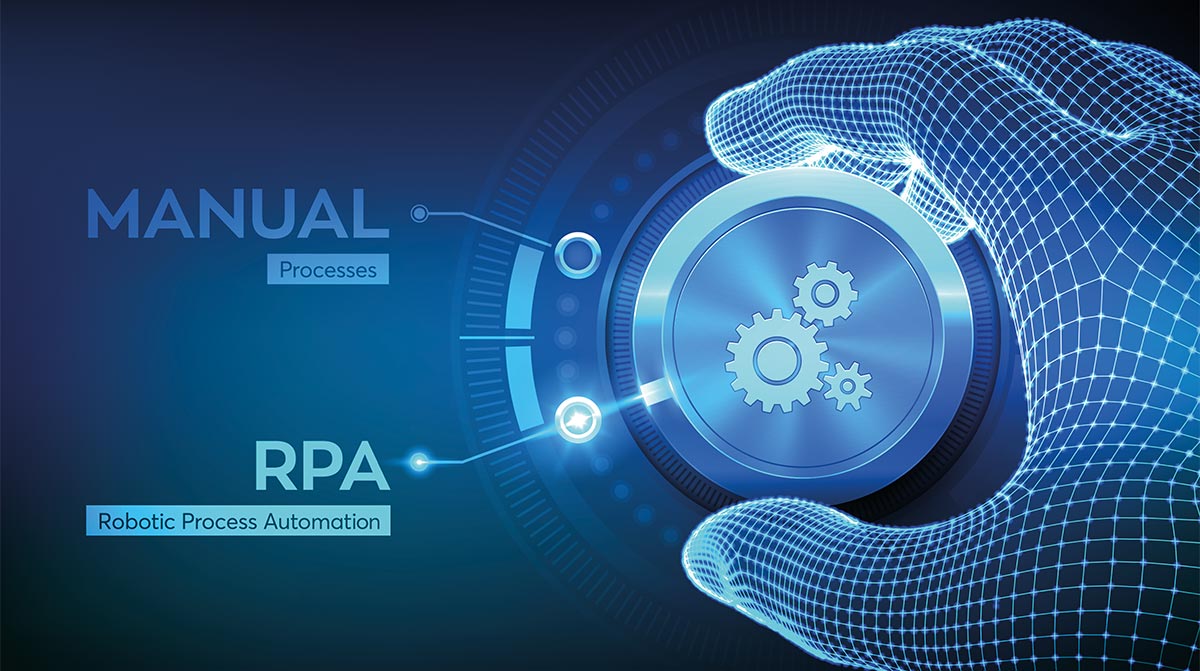
INDUSTRY 4.0 EXCELLENCE
Smart analytics, RFID trackers or customer portals: Which investment actually pays off in which timeframe? This project was about mastering an Industry 4.0 transformation in twelve months. First, EFESO designed a target image for the overall architecture via an Industry 4.0 assessment and showed ways for the Industry 4.0 transformation to exploit existing resources. The company then put several new applications and methods into practice.
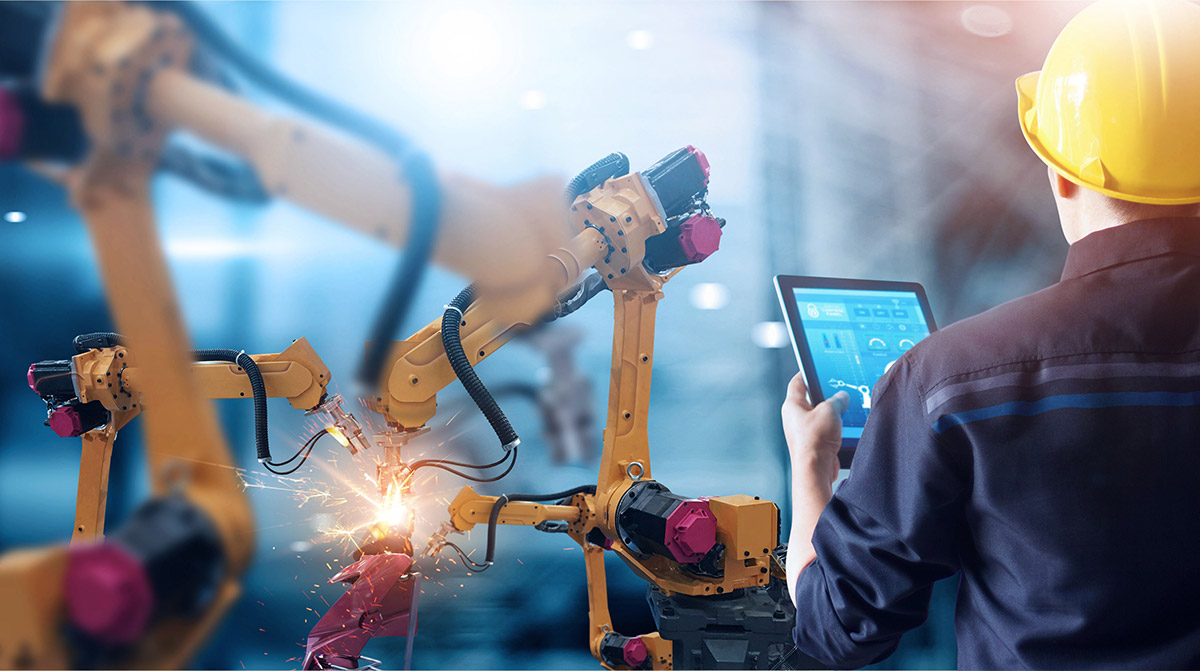
SMART FACTORY PLANNING
Will products in the ideal factory of the future control their production completely independently? Or should the focus rather be on the perfect choreography of people and machines? In this case, a company developed four of its plants in Europe into "smart factories". EFESO determined the status quo in terms of digitalization and Industry 4.0 with its Smart Factory Scan and created development scenarios and location strategies. In addition, the project team classified key topics and initiatives for each location in a portfolio for possible Industry 4.0 pilot projects.
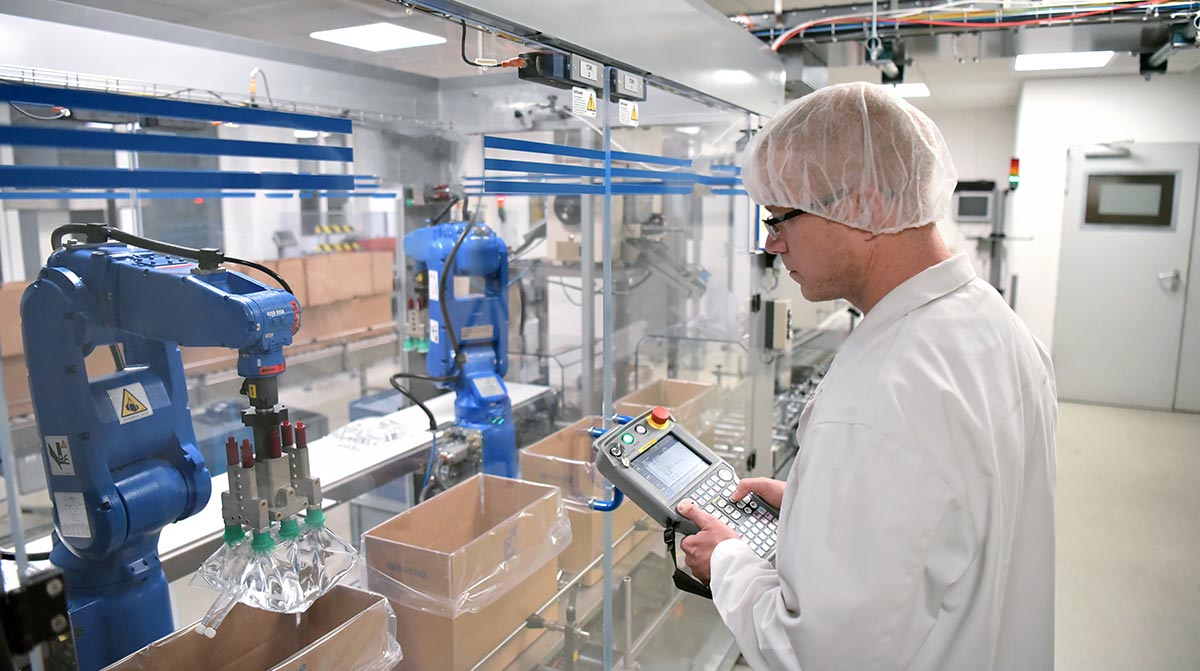
DIGITAL SHOP FLOOR MANAGEMENT
With an automotive manufacturer, EFESO created a best-practice model for digital shop floor management in two plants with the goal of expanding this approach to approximately 50 plants globally and thus achieving optimal networking of all shop floor information. In this way, improvement initiatives were to be initialized more quickly and efficiently, and the plants were to be comparable with each other on the basis of uniform key figures. This is exactly what an IoT platform with a uniform reporting system made possible. In addition, all collected data can be aggregated at any time, from the machine up to the plant management.
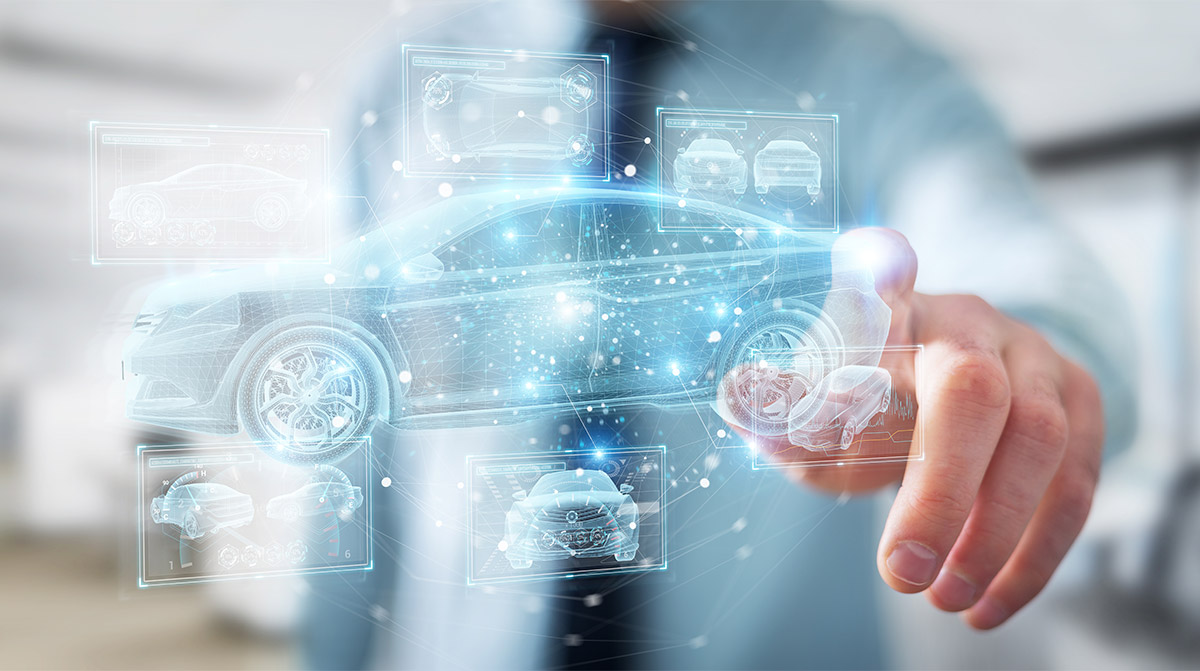
END-TO-END DIGITIZATION
How do digital tools create a customer journey with a wow effect? Especially when a company with several brands is very broadly positioned, the uniform design of an end-to-end process to the customer is a critical aspect for success. EFESO used parallel front-end and back-end teams to solve this task. These ensured that product customization worked from the point of sale through manufacturing to product delivery. Thanks to the company's high affinity for digital applications, the processes were successfully restructured across all sales channels and for all brands.
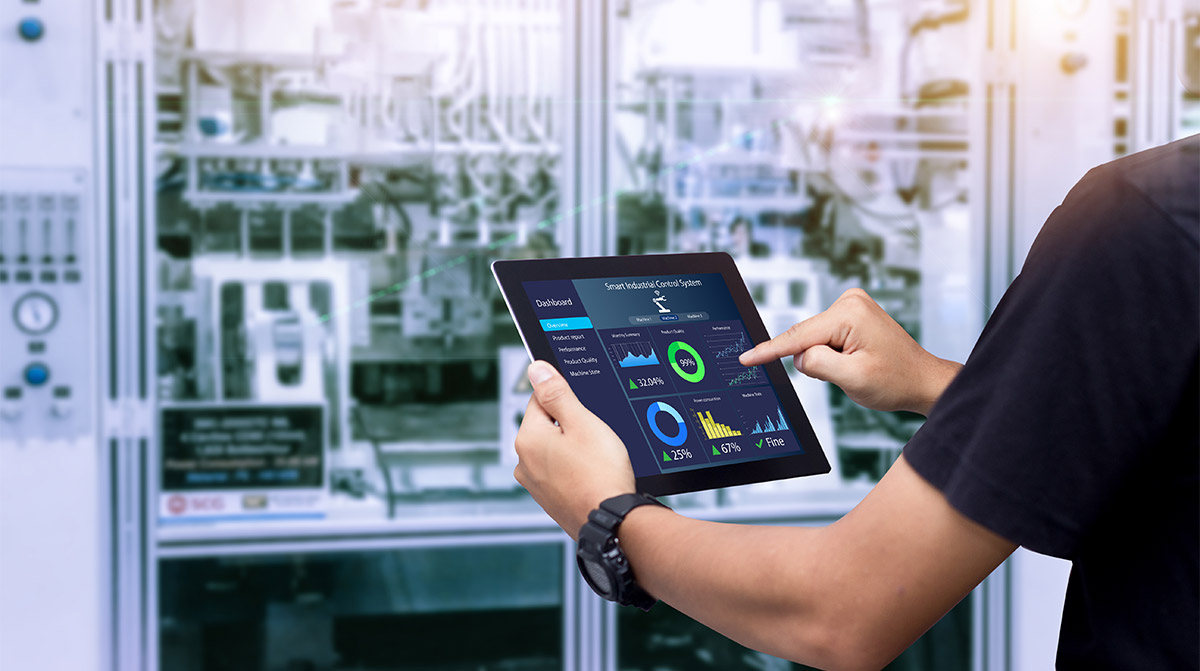
DIGITAL PROCESS TWIN
With a digital twin, not only products but also processes in production can be simulated. In this case, EFESO was to reduce the reject rate of the high number of variants in production. To this end, the project team analyzed which process parameters influence performance and quality results. Based on the collected data, a "Digital Process Twin" was developed in a cloud application. This monitors the physical process in real time and thus provides a virtual cockpit for value stream management.
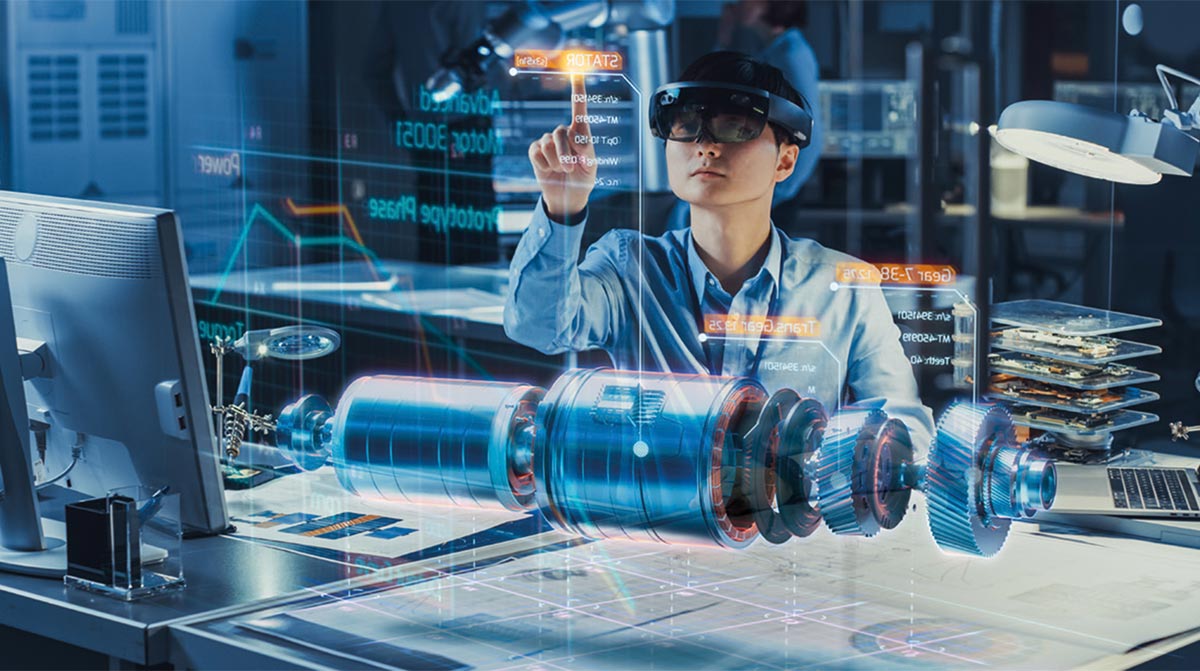
FUTURE FACTORY
EFESO accompanied the development of a customized factory of the future for a manufacturer of special equipment - from the drawing board to the handover of the keys. The focus was on increasing the quality of the products, reducing costs and making projects plannable. The factory was created using three strands of action: the design of the physical elements, the design of the information flow and the management of these two tasks. Using cloud technologies, the company was also able to implement an interface-free fusion of the digital and physical worlds.
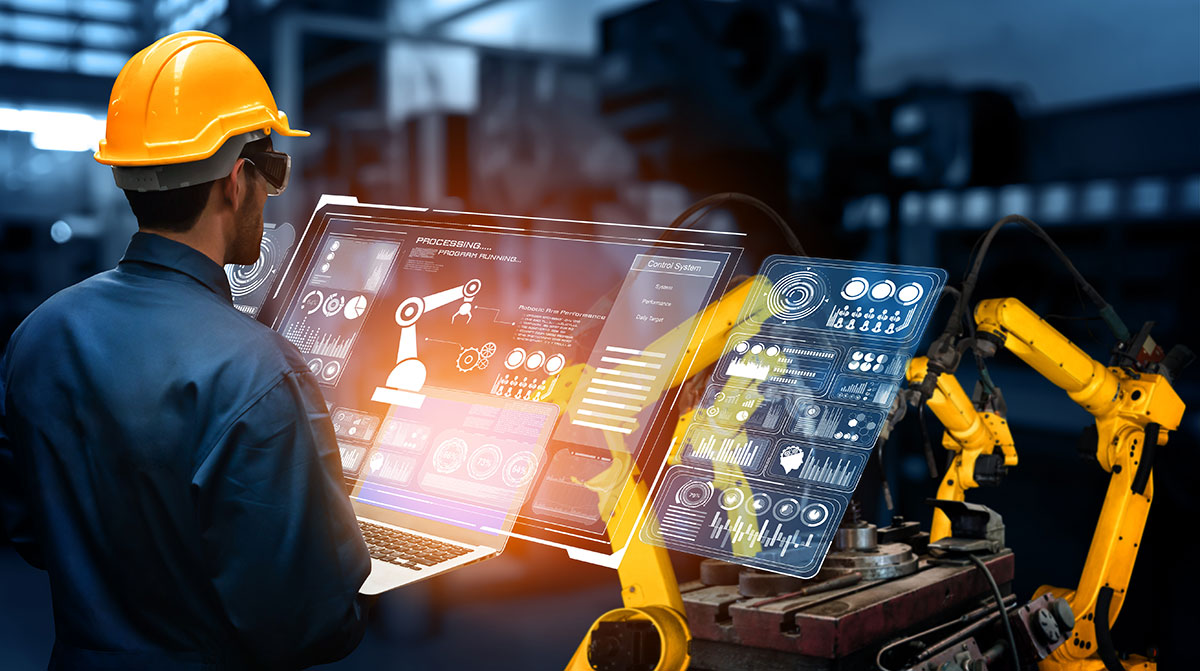
SMART-PRODUCTS-DEVELOPMENT
A series developer realigned its Product portfolio to smart products. EFESO supported the necessary change process by setting up three teams in the company. In this way, the different competencies and perspectives of "digital immigrants" and "digital natives" were united in the organization. A key success factor proved to be creating tangible results, e.g. with valid prototypes, in order to bring skeptics and observers along.
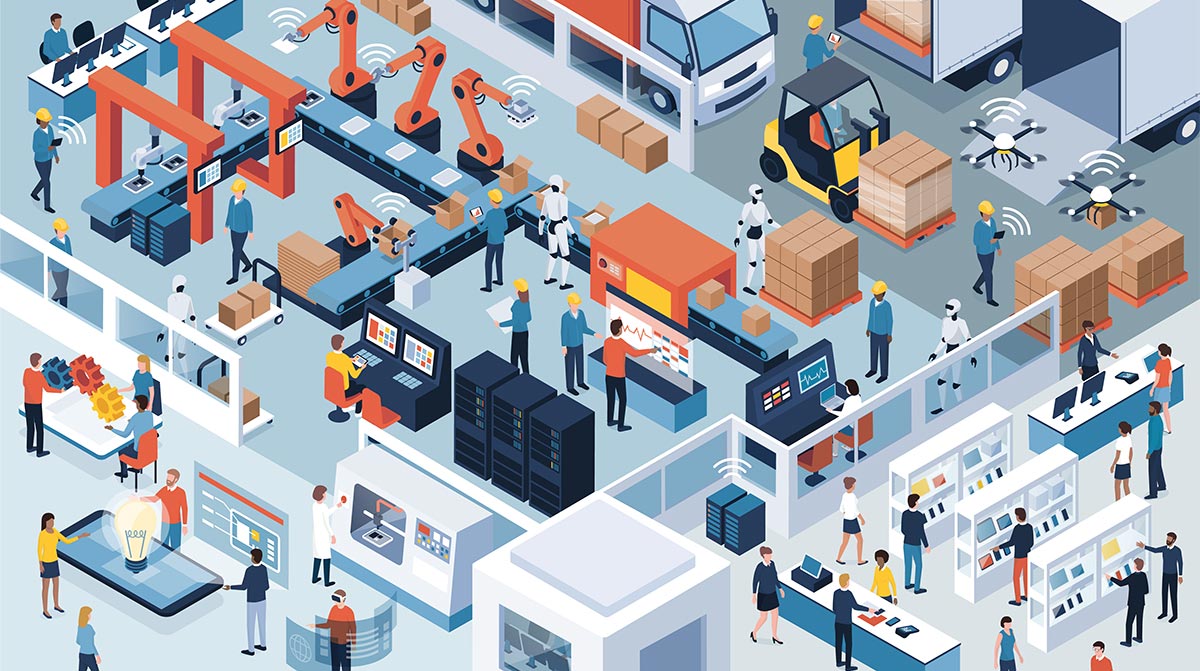