ON THE WAY TO "SCREENTIME ZERO"
As a subsidiary of Pepperl+Fuchs, a manufacturer of automation technologies, we develop Industry 4.0 solutions for the intralogistics of medium-sized companies. In this case, an automotive supplier commissioned us to make the delivery or provision of parts to its production lines as "lean" as possible. The goal: "Screentime Zero" - no worker should have to log on to a computer to book parts.
The company decided to digitalize its inventories and shelves in intermediate warehouses, which were already organized using Kanban. For this purpose, the processes were to be analyzed and optimized, and a complete solution was to be created that could also be integrated into other, already existing production or intralogistics environments.
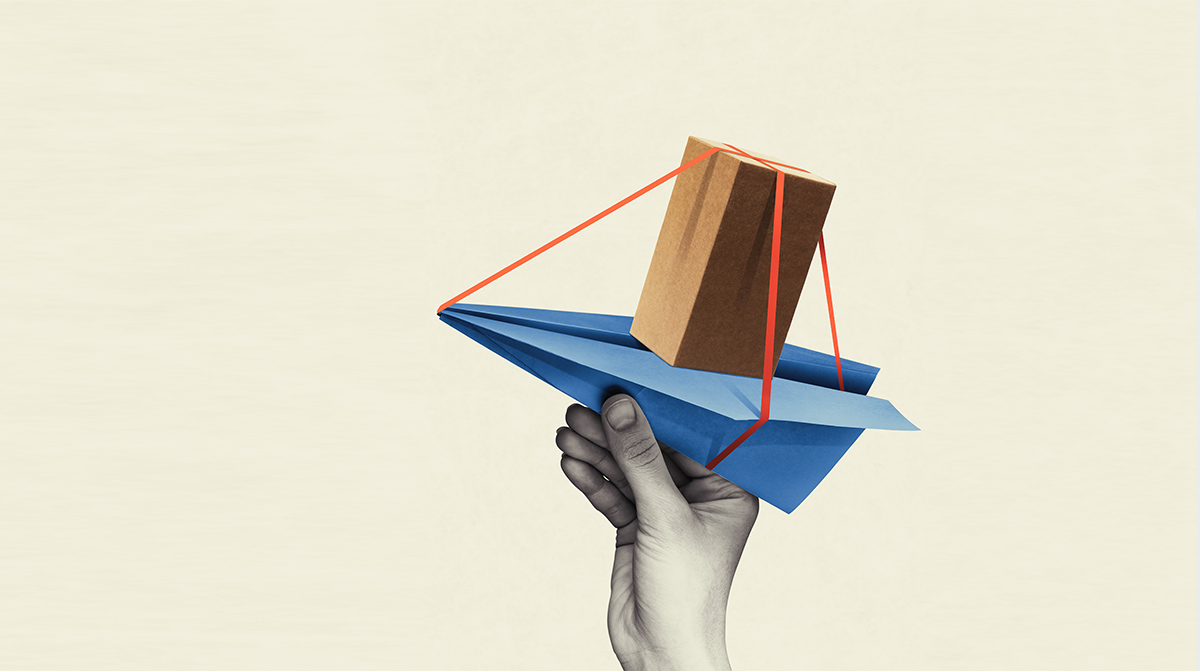
Smart shelves: Detect material movements and process them intelligently
To solve this task, we combined three technologies to create a customized IIoT solution: In addition to RFID systems for identifying containers and material, this solution uses sensor strips specially developed for Kanban shelves to precisely locate and detect material movements in shelves. The data obtained in this way is processed using process-oriented cloud software.
All in all, we were able to fully digitalize the company's kanban-based value chain. This not only ensures more transparent, more efficient processes in the intermediate warehouses, but also enables the digital registration and "smart" processing of all material movements. In addition, a synchronous, digital image of the shelf stock can be created at any time in the cloud-side backend. The following functions and application examples illustrate how the solution works in detail:
Material staging with order-specific entry
In production, four forms of staging are common: The classic method is Kanban, i.e. , the material is always on the line and as soon as demand arises, a signal is sent to the source in the warehouse. Other options are just-in-time production, the tightened variant just-in-time sequence and finally order-based picking. Our solution can support all four forms.
If there is a very large number of variants, it does not make sense to always have all materials on the line. In this case, we offer a hybrid solution and combine Kanban with order-specific provisioning. When the worker scans his Manufacturing Order, Kanban materials are in stock, but also a container with the order-specific components. For the logistician, this is exactly the same workflow, but it is controlled differently by the logic in the system. Since the manufacturing orders for the next few days are stored in the system, order-specific materials can also be staged on the line that would normally only be staged at the start of the order.
Material supply with automated picking orders
In every production line, material supply at the interface between warehouse/intralogistics and production is an important starting point for process improvements. For smooth workflows in the line, the right material should be available at all times in the (kanban) intermediate storage. Otherwise, missing components have to be removed manually from the warehouse, which can take up to 30 minutes and costs valuable productive time for the worker. Manual picks that are necessary several times a day reduce overall efficiency enormously. We solve such situations by registering every pick from the Kanban shelf and, if necessary, the IIoT solution triggers a picking order in the warehouse, without any intervention from the worker. This works via optical sensor strips that are installed in the shelves and track every material movement.
Material flow control with anonymous containers
Another aspect is material flow control. Many of our customers work with Kanban containers that receive a fixed allocation to the material. When the material is used up, the exact container is returned to the warehouse and filled again with the same material. Our approach is to anonymize the containers instead, i.e., the picked material is newly paired with an anonymous, empty container of the same size, to which the corresponding virtual Kanban ID is assigned. Thus, processes can be parallelized and replenishment times can be reduced enormously. Depending on how far the warehouse is from the line, this can range from half an hour to half a day. Faster replenishment also reduces buffer sizes, saving valuable space in production. In various application scenarios, our customers have thus been able to extend their production by up to 10%.
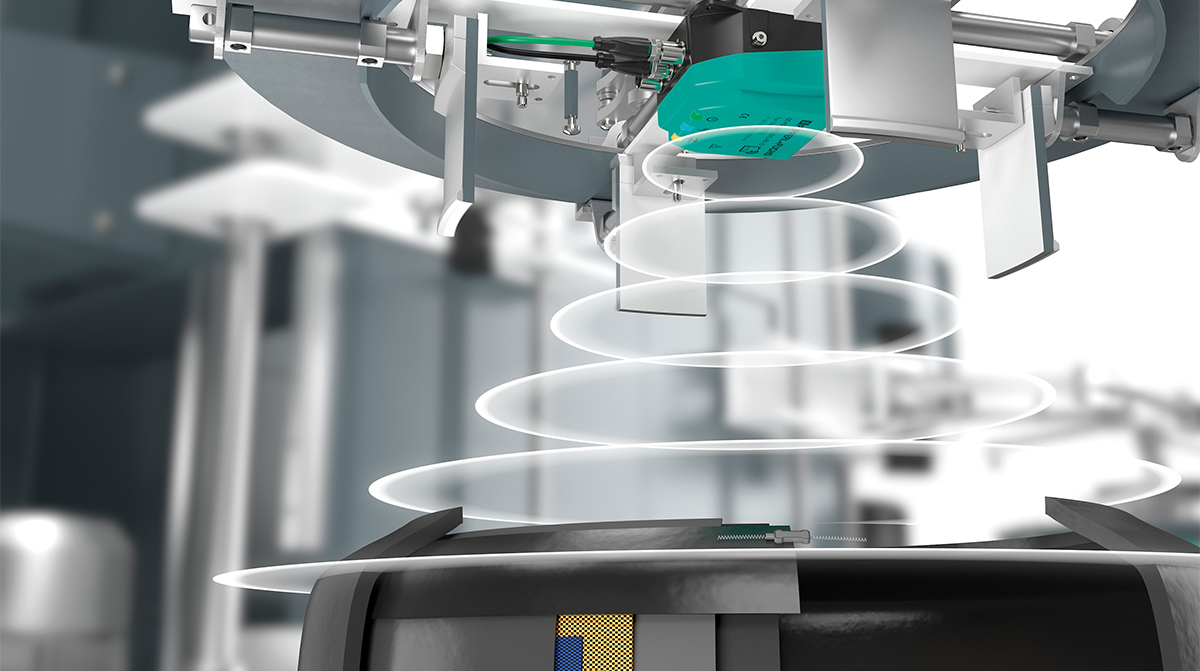
Parallel supply processes reduce costs
In addition to the aspects mentioned, the solution also positively influences process stability and product quality. This was demonstrated in the case of another customer who manufactures highly individual control cabinets whose components are very similar: In order to avoid mix-ups during assembly, the worker is shown how many elements of which type he has to pick when scanning his Manufacturing Order at the shelf compartments via "Pick by Light". To avoid errors on the put side, where the materials are loaded, the logistician scans the bin. The correct aisle is then displayed and he inserts the parts there. The system then books the container in exactly the right position.
Concrete results from the application of the IIoT solution are, for example, a reduction in working capital along the entire process in the plant of up to approx. 20%. This is achieved primarily through the continuous material availability and a dynamizable material provisioning. But also the manual effort for the material search is reduced by several minutes per production order. The lead time for logistical material supply processes can be reduced by up to half, depending on the distance between the warehouse and production. This is made possible primarily by supply processes that now run in parallel, as these can be initiated automatically. In addition, the space required for shelves near the assembly area can also be reduced by up to approx. 20%, as the material is provided on a consumption-oriented basis.
In the future, further modules such as an "RFID to Cloud" service are to be combined with the material flow control described to form a comprehensive Intralogistic Solution Suite. RFID reading heads could be positioned at any point within production and trigger business processes. For example, a transport order could be acknowledged fully automatically in SAP as soon as a forklift passes through an RFID gate. There is therefore still further potential for implementing "Screentime Zero".
Field of application: Automation/Intralogistics
Challenge
Digitization of the kanban-based value chain of an automotive supplier with the goal of increasing process efficiency in intermediate storage and achieving "screentime zero" in the work steps of employees.
Solution
Recording of all material movements with a specially developed combination of optical sensors and identification systems with cloud software; better management of intralogistics processes in the plant through digital visualization of shelf stock in real time and direct integration into the ERP system.