Sustainability has become a key factor in the investment decisions of chemical companies
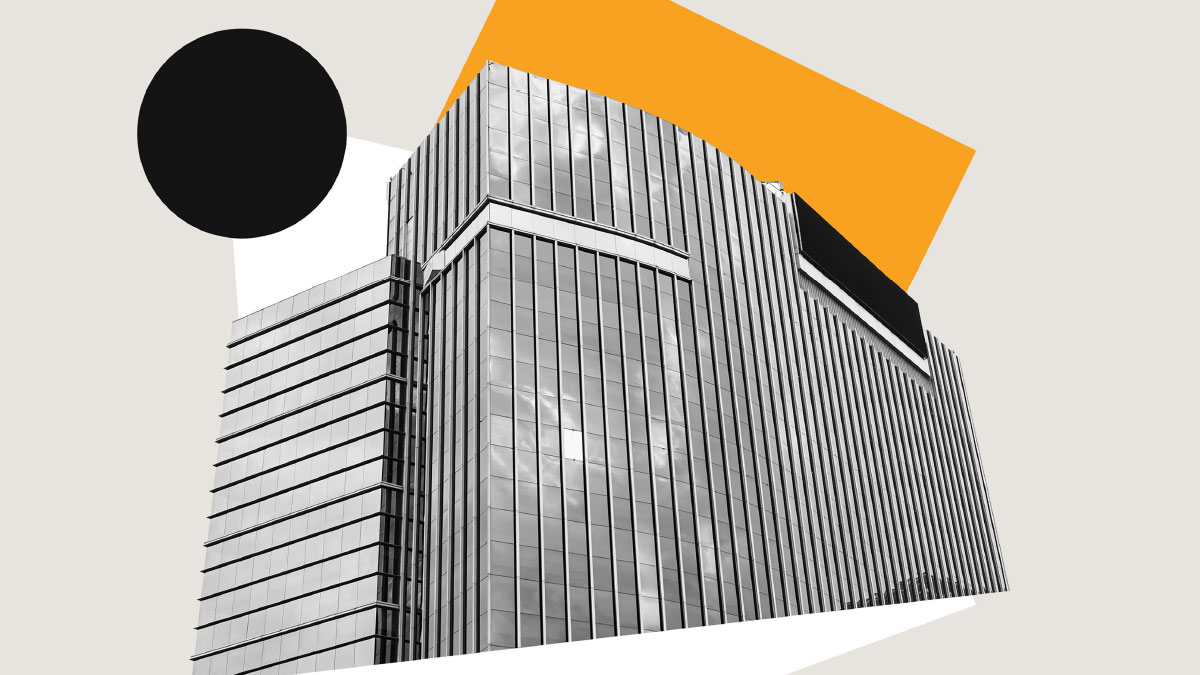
Interview with Fernando Cruzado, Vice President & Industry Lead Chemicals, EFESO
DIALOG: How important is the topic of CapEx optimization for chemical companies?
FC: Investment decisions in the chemical industry tend to be long-term in nature. This is due, on the one hand, to the complexity and long planning and realization times for the construction of systems and, on the other hand, to the high investment costs involved. Companies, therefore, often focus more on the total cost of ownership (TCO), which also includes environmental factors such as industrial policy incentives, long-term energy cost expectations or available skillsets at the planned location. Simultaneously, chemical companies often operate in very different market environments each requiring a different focus and balance between OpEx and CapEx.
DIALOG: What basic strategies can be observed?
FC: Of course, every company will strive to optimize and use CapEx funds as effectively as possible. In our experience, three basic patterns can be distinguished in terms of focus, each of which is characterized by a different market logic. First, the more stable and predictable in the long term, e.g., a market, the lower the initial investment costs compared to the ongoing costs for the profitability of the business area. Therefore, companies operating in such market environments will be more willing to accept higher investment costs in favor of better maintainability and lower maintenance costs for their systems. Second, companies in more uncertain or cost-sensitive market environments will try to reduce CapEx in order to invest in new systems or processes, even if this sometimes means higher maintenance costs. And finally, there are areas in which the speed with which a company can bring a product to market and thus secure market share is decisive – rather than the level of initial investment costs. We have seen examples of such an agility-driven market environment during the coronavirus crisis, where speed was the order of the day.
DIALOG: Apart from these “winner-takes-all” markets, the main issue is therefore the trade-off between initial investment in engineering and the costs of operating the systems. Which factors should be considered in terms of a comprehensive TCO analysis?
FC: In the past, a very close eye was usually kept on the key financial figures. Today, a much more comprehensive approach is taken. In addition to the actual running costs for maintenance or operability, this increasingly includes sustainability aspects such as energy efficiency or the CO2 emissions of systems, which are included in the evaluation of investment costs in the form of sustainability coefficients or scoring.
This means that by quantifying these environmental factors, which have been given less consideration in the past or were not calculable at all, a certain compensation can now be created to justify higher CapEx for investments in more sustainable structures. In other words: sustainability has become a key factor in the investment decisions of chemical companies. In some companies, access to CapEx funds is strictly linked to contributions to sustainability goals.
DIALOG: What levers can companies in the chemical industry use to directly influence costs in the CapEx environment?
FC: There are various starting points for reducing CapEx when building new plants or expanding existing ones. It is crucial for effective optimization that the engineering teams are prepared to question things actively. Typically, this is done in cost-down workshops in which, based on the specifications, a minimum solution is examined to determine what is functional, sensible and necessary. This concerns both the correct dimensioning of the systems and the specification of the requirements. Further starting points typically arise wherever “external” requirements are introduced into the engineering process – for example, in safety. There can be no compromises when it comes to safety-critical elements. At the same time, a pragmatic translation of the safety requirements into system design is mandatory – with the aim of designing safe and operable systems. In addition, there is potential in the actual execution as well as in cost engineering, i.e., the detailed scrutiny and benchmarking of cost structures. The latter is less pronounced in the chemical industry compared to other sectors, as the focus is on delivering functioning systems on time.
DIALOG: What role does digitalization play in this?
FC: Digital technologies can safeguard investments by digitally simulating the effects of certain measures before investing in physical infrastructure or adapting a chemical process. On the one hand, this relates to process engineering, where a digital twin can be used to simulate the effects of certain parameter changes, such as pressure or temperature, on the chemical reaction. On the other hand, 3D models can be used as part of plant planning to involve not only process technicians and plant engineers but also representatives of the shop floor in the planning process at an early stage. This makes it possible to identify planning errors instead of having to correct them later with high CapEx input.
Interview partner
Fernando Cruzado, Vice President & Industry Lead Chemicals, EFESO
In more than 20 years of consulting experience, Fernando Cruzado has led numerous transformation programs in sectors such as the chemical and process industries. He has extensive experience in setting up and managing global OPEX programs. He also focuses on organizational development and the design and implementation of industrial footprint networks.