CapEx potential can only be leveraged if you consistently break away from the old
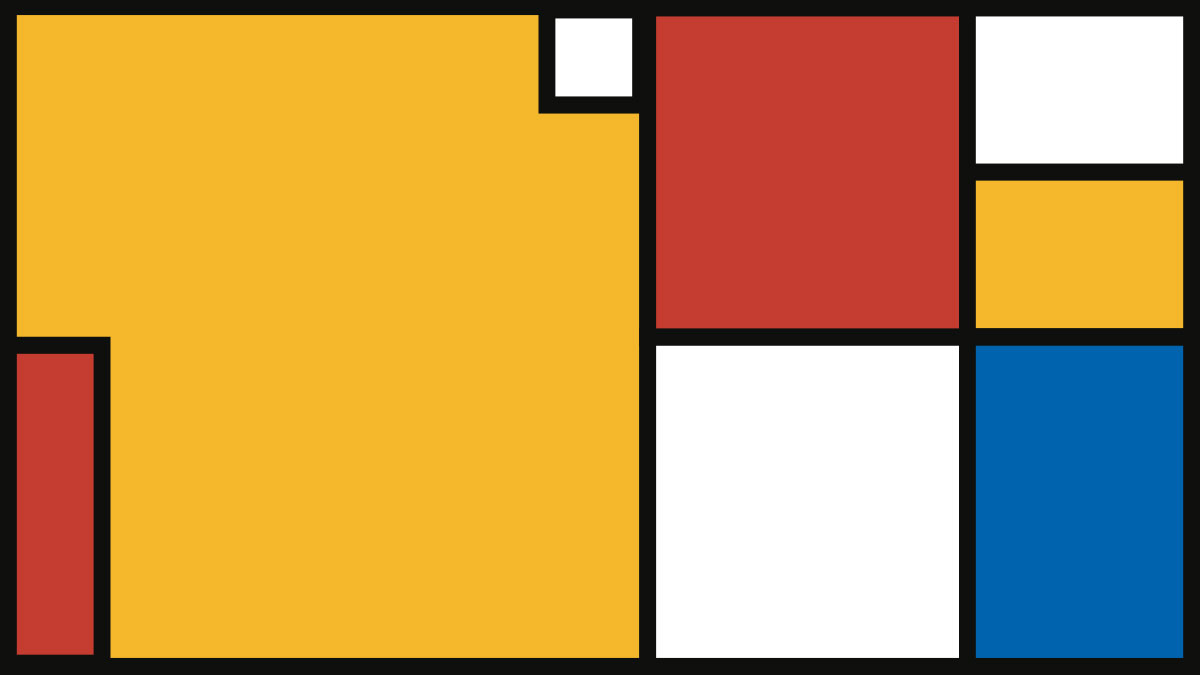
Interview with Dr. Christian König, Principal, EFESO
DIALOG: Sustainable cost reduction focuses on both operating costs and long-term investment costs. What are the main differences in the approaches?
CK: A significant proportion of CapEx goes into buildings and systems, which requires a different approach to traditional process issues. Because once the investment has been made, you must deal with the circumstances – and focus on better utilization. CapEx initially arises when new investments are made. For example, several gigafactories are currently being built around the world, which also entails investments in associated infrastructure, development centers and much more. However, the necessary replacement and improvement investments are also important, often in connection with rationalization. This applies, for example, to machines that could still be used to produce – but not as well or as quickly as with new systems.
DIALOG: What approaches can be used to avoid long-term investments?
CK: A key lever is the consideration of capacity. CapEx is often driven by an assumed capacity requirement, such as new machines. An important question is, therefore, whether the existing range of systems is being used efficiently. The first thing to look at here is Total Effective Equipment Performance (TEEP). This is because existing capacities often stand idle for a long time, are poorly maintained, are set up for a long time, or defective products are created that do not need to be created at all. The same approach also applies to productivity per unit area. Of course, too much consolidation and an intensive workload can also lead to a breakdown and ineffectiveness. An appropriate balance is important here.
Another interesting aspect is the differentiated view of automation. The trend in the industry has been towards high automation for many years. This also included products for which this is not necessary, especially if production was outsourced to best-cost countries at the same time. Today, more and more companies are questioning this trend. New approaches are emerging here, such as flex lines, which can be staffed with additional employees if needed. Those lines require much less investment.
DIALOG: What is the significance of outsourcing in the CapEx context?
CK: Outsourcing is an important instrument because not every investment is right and necessary in the long term. From a business perspective, it can certainly be worthwhile to fully utilize your own facilities and cushion the peaks with external manufacturing partners. In some cases, the costs of constructing buildings can also be outsourced. In certain situations, it can therefore make sense not to have to make the investment yourself.
DIALOG: Does the perspective on CapEx change when the entire network is considered?
CK: A cross-location perspective reveals considerable untapped potential in some cases. Companies that operate several development or production sites often have over-capacities globally. This raises the question of whether capacities can be managed correctly worldwide, or at least regionally, and whether requirements can be distributed within the manufacturing or development footprint. A high level of transparency regarding all relevant facts and indicators is crucial for this. Digitalization also plays a decisive role. However, the “fluctuation” of capacities in the network has certain limits. For example, if a company has a new plant in Eastern Europe and benefits from considerable labor cost advantages, it will not automatically shift production towards capacities that are available in principle at a high-wage location. It is crucial to take a very detailed look at the actual current expenses, e.g., for manufacturing product and development costs, but also for coordination, the supply chain, transportation, taxes, and fees as well as potential risk costs.
DIALOG: What role does product design play in CapEx considerations?
CK: The motto here is “Design for Smart Manufacturing”, so that cost-effective production is possible later on. A second important point is “Design to Line”. This means designing new products in such a way that they can be manufactured on existing systems. This is not always the case. Completely new systems are often acquired with each product generation, and existing systems are relegated to a shadowy existence for a few spare parts. This is due to the lack of networking between production, engineering, and R&D.
DIALOG: Is it possible to go too far in reducing and limiting CapEx
CK: A certain amount of excess capacity is important to remain flexible and agile. Because inflexibility can be detrimental to business. For example, if a downturn in demand has a temporary nature, the ability to deliver must be maintained. Otherwise, you lose market share when the engine starts up again. Another factor is the avoidance of single sourcing and deliberate risk diversification. The importance of this strategy has been made very clear to us in recent years during the pandemic and other global crises.
Interview partner
Dr. Christian König, Principal, EFESO
Christian König supports companies in their digital transformation. Together with his clients from the manufacturing industry, he focuses on process and IT harmonization. He also prepares companies for the future with Industry 4.0 assessments and efficient supply chain management.