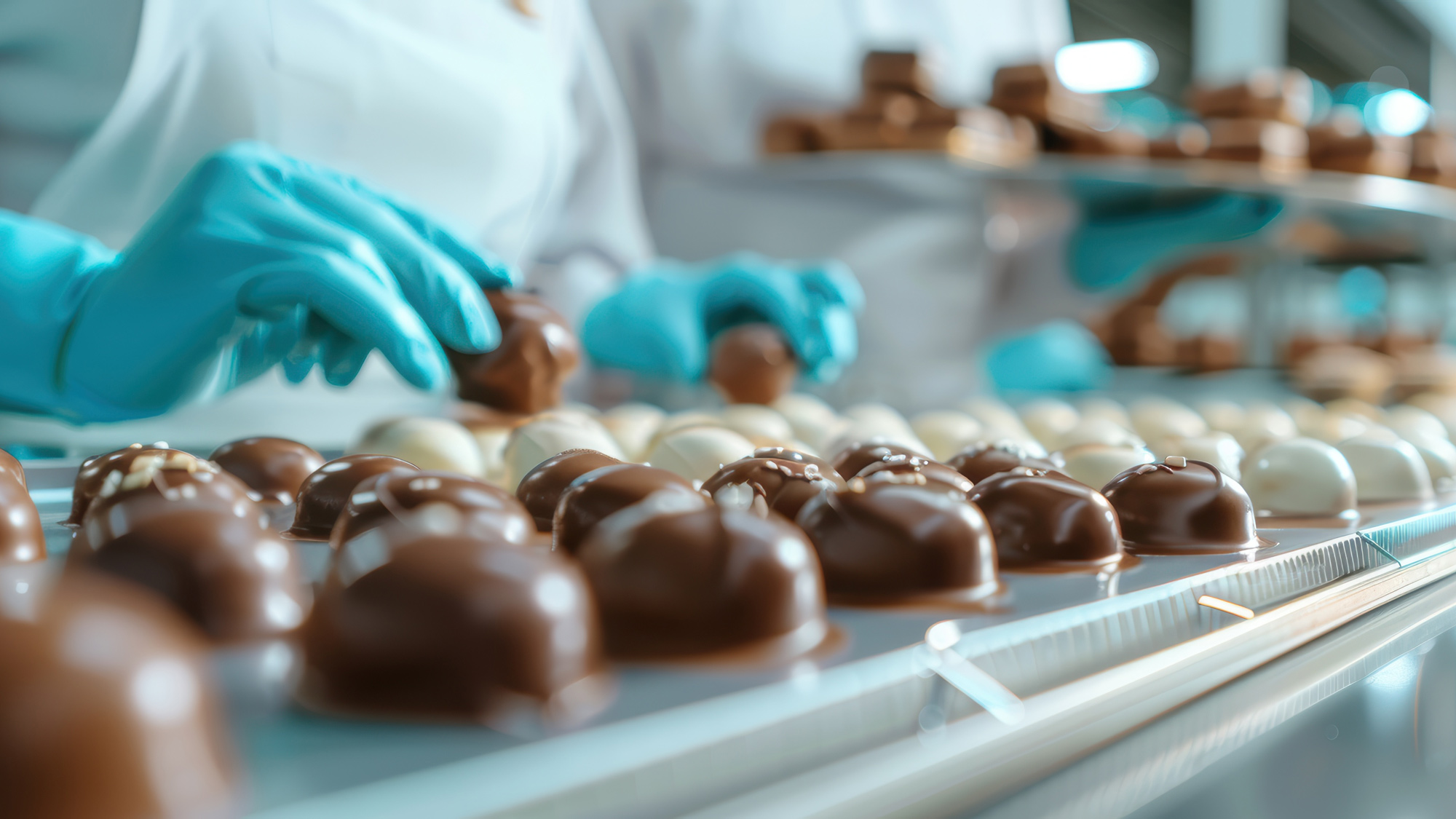
On the road to digital excellence
Digitalization as the key to increasing efficiency in chocolate production
How do you produce in a resource-efficient and profitable way in an intensely competitive market - without compromising on the highest quality standards? This was the challenge facing a chocolate manufacturer whose products are popular all over the world. The long-established company has been extremely innovative and future-oriented since it was founded. In order to continue this success story with the digitalization of several plants at international locations, he brought in the expertise of EFESO.
Together with the EFESO consulting team, the company developed its first group-wide digitalization strategy and determined the personnel and technological framework conditions for its implementation. Additionally, the project team summarized in a globally applicable roadmap, which technologies are best suited to be used in the plants – with a significant impact for their digital transformation.
Challenge
A chocolate manufacturer started its digital transformation with EFESO. With a Group-wide digitalization strategy and a roadmap for its global implementation, the project team laid the foundations for activating potential in production and logistics with the right technologies.
MOREEFESO solution approach
The project team carried out assessments and identified the most beneficial digitalization initiatives for each plant. At the same time, it used a GAP analysis to show the current and future skills required in a digitalized world. In addition, 20 use cases named specific technology options.
MOREEFESO success model
Previously autonomous work and functional areas were networked with each other, and the exchange of information was promoted. With use cases and digital initiatives, target KPIs are used to show how these can be realized in sales figures and efficiency or quality results.
MOREGlobal increase in production capacities
The global, originally decentralized organizational structures of the company played a key role in the initial situation of this project: a team at headquarters managed the production volumes of the network of ten factories. Priority was given to the cost- and quality-oriented transfer of the production of standard goods from plant to plant. At the same time, the factories were locally responsible for topics such as operational organization, HR management and their IT/technology infrastructure. This led to the following challenges:
- Long lead times and a lack of transparency for and in the product development.
- Limited ability to react to price increases for commodity products in local markets; these products should also be used more efficiently.
- In-house and therefore different standards for quality controls.
- High manual effort in manufacturing planning and control.
The increasing popularity of the chocolate brand with customers around the world raised the pressure to act on these issues. In order to meet demand quickly, production capacities should not be enlarged through expansion, but rather by increasing efficiency in the plants. The digitalization of the factories quickly proved to be a key factor in this. Although the company had already closely networked his production facilities, they were not yet utilizing the full potential of the collected data, e.g. in order to optimize their production processes to increase the frequency of the lines. The project team of EFESO consultants and operations managers defined two tasks for the digital transformation, which was to be implemented in several plants in parallel:
Task 1: Development of a global digitalization strategy
The degree of maturity of digitalization and IT/IoT infrastructures varied from plant to plant, as these topics were also driven forward locally. The first task for the project team was therefore to create a binding framework for action for all plants with a holistic digitalization strategy and the definition of an overarching IT/IoT architecture. This required a clear assignment of roles and definition of responsibilities for these topics – both within the plants and between them and the Group.
The project team calculated a ROI of less than two years for the digitalization measures.
Task 2: Creating a roadmap for implementing the strategy
Based on the operations areas of production and logistics, the project team also identified the methods and milestones for implementing the digital transformation in the selected plants. In this situation, the company benefited from the successes it had already achieved in previous years with EFESO in Operational Excellence (OPEX) programs. The project team calculated an average ROI of less than two years for the digitalization measures to increase efficiency in production and logistics.
The project was launched at a time when food producers around the world were stepping up their activities and investments in line with "Industry 4.0". The chocolate manufacturer had already gained a competitive edge in this area, as it had been using a knowledge database and digital method toolkits from EFESO for years. The project was therefore launched at the ideal time to realign the production processes, systems and connected work processes across all plants in the direction of "digital excellence".
Coordination of strategy and operationalization
In this case, the Group management generally recognized the great value of a common, overarching vision that is shared by all locations and that allows them to learn from each other in the implementation of this vision. Together with the senior management team, the project team launched the digital transformation in two stages:
Stage I: Digitalization strategy
- Strategy scope: The project team defined the most important financial and strategic fields of action for the digital transformation. All results and activities that took place in the course of the project - and will take place in the future - must be clearly linked to one or more of these fields.
- Actual and target value: In order to capture the status quo of digitalization, the project team assessed the digital maturity level of the plants and determined which further digitalization initiatives are particularly promising there. In addition, a GAP analysis revealed not only the company's current capabilities, but also those required in the future in a highly digitalized world.
- Personnel and technological infrastructure: With a detailed organizational structure for the digitalization team, clear and binding roles were created for the implementation of the strategy. The project team also drew up a concept for developing the necessary technical solutions and defined the appropriate future IT architecture.
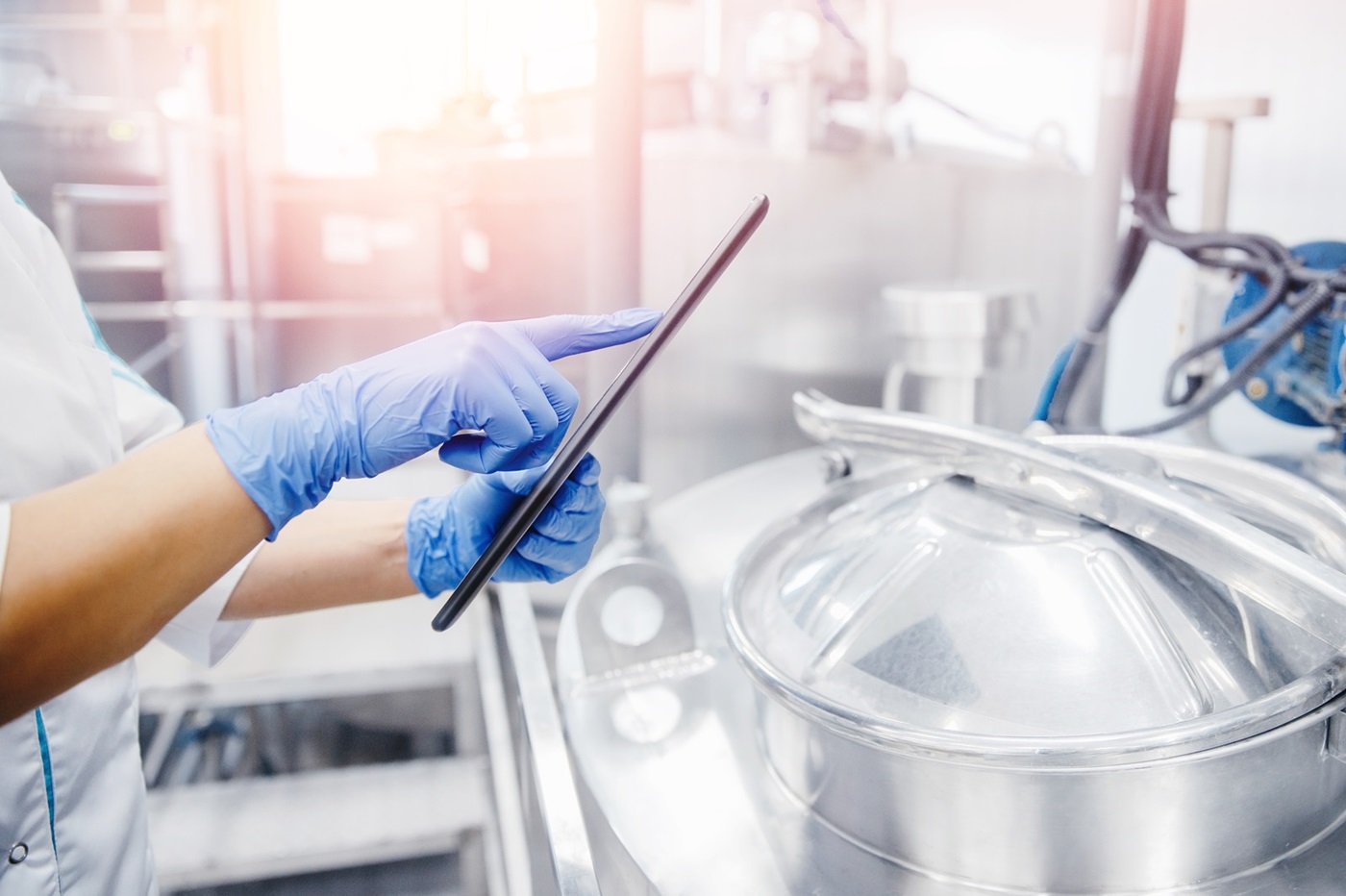
Digital In-line Quality Control
- Identification and definition of requirements.
- Connection of existing and integration of new measuring devices in production.
- Configuration, data integration and test runs.
- Training and roll-out.
- Adjustments based on experience, implementation in other lines or plants.
Targeted qualitative results: Real time visualization of quality level, higher rate of quality checks, higher accuracy.
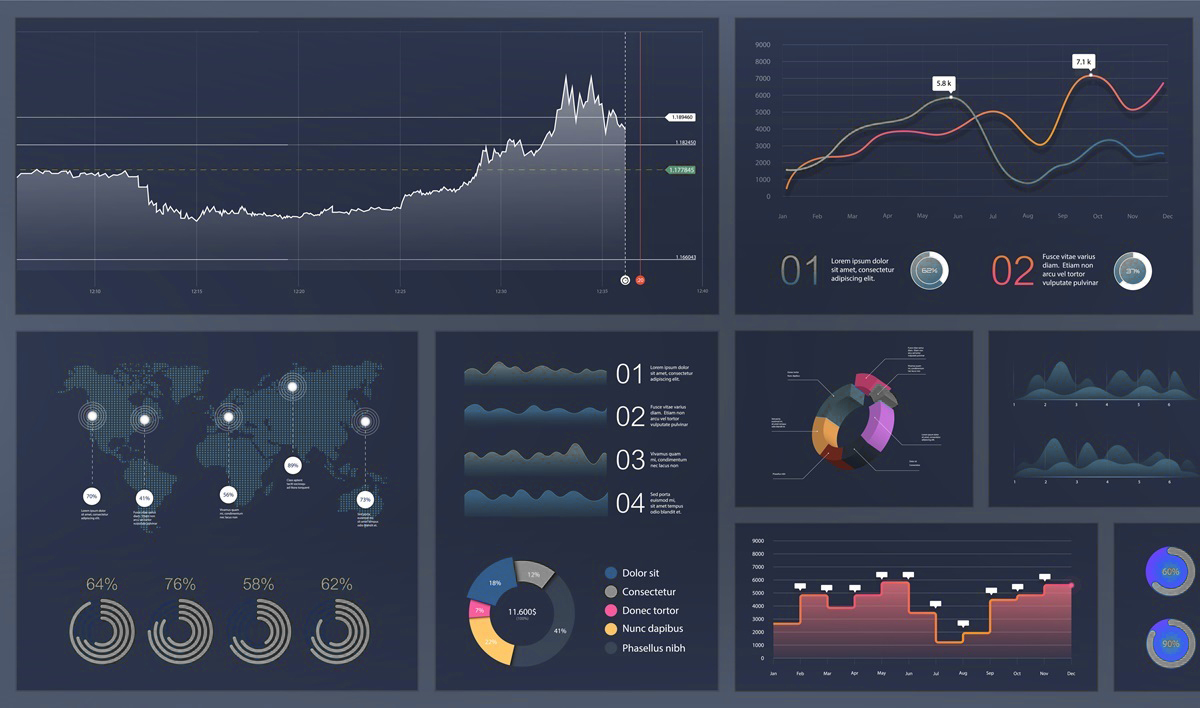
User-friendly analysis tool
- Development of an ideation and delivery model for analytics, incl. core team.
- Requirements elicitation incl. interfaces.
- Selection and implementation of the tool.
- Development of integration (connectors) to third-party systems, development of initial analyses.
- Training of core users.
Targeted qualitative results: Better decision making and faster problem solving, more effective use of existing data.
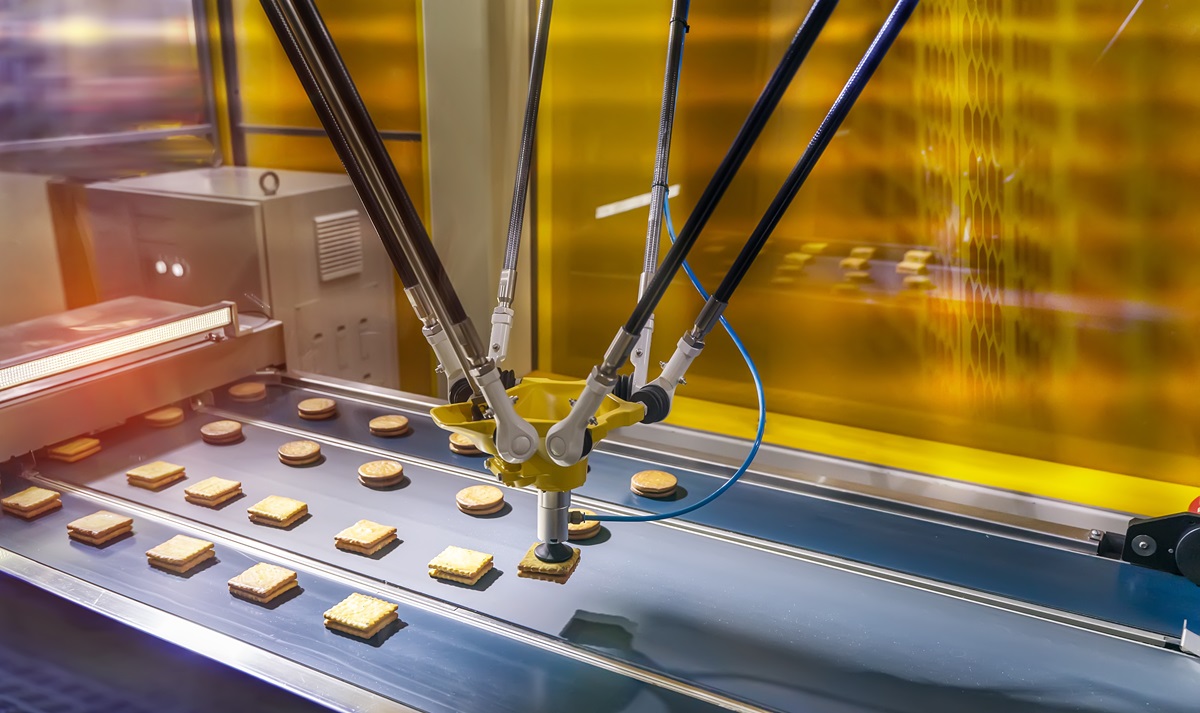
Autonomous Process Control
- Definition of the project scope and objective.
- Implementation of hardware.
- Creation of a system based on machine learning.
- Training and roll-out.
- Return of experience and start with step 1. for the next department.
Targeted qualitative results: Better decision making and faster problem solving, more effective use of existing data.
Stage II: Roadmap for strategy implementation
- Digital factory scan: The project team expanded the results of the digital maturity level with a detailed assessment of the processes and the technological maturity level of the individual plants. It also identified the need for action in the event of gaps in skills and knowledge.
- Use cases and IT target image: The company was given 20 use cases of Industry 4.0 / digitalization technologies to choose from, which addressed the main areas for improvement in production and other operational areas of the plants (see following examples). Some of the technologies were already successfully used in the industry, while others were innovations that precisely matched the needs of the plants. This was supplemented with a target image for the IT infrastructure.
- Roadmap: A roadmap for implementing the digital transformation in the plants within four years was created based on the points mentioned.
In this case, EFESO was already very familiar with the processes and players, as it had been involved in improvement projects, e.g. during the introduction of the PCS system and in carrying out loss analyses. Employees at all hierarchical levels were highly motivated to drive forward a Continuous Improvement Process (CIP) and to regularly measure and improve the performance of the plants in an internal, global competition. EFESO flanked this with corresponding projects in production, logistics, product development and cross-divisional change management.
The roadmap for implementing the digital transformation was drawn up for four years.
Establishing a progressive corporate culture
In the course of the project, the following points have been proven as critical to success:
Build trust!
The exchange with HR managers is often underestimated and neglected in comparable OPEX and digitalization projects. Understanding and shaping communication is just as important as understanding operational processes - especially during transformation phases. How do you involve employees properly? How do you communicate goals and results in a way that promotes trust and team spirit? To successfully resolve these issues - first at the top management level and then at the functional levels of the plants - early cooperation with HR is essential.
Promote sporting competition!
The company had already established a knowledge and KPI-oriented learning culture in the plants before the digital transformation. The successes achieved in the OPEX programs were backed up with training and shared within the plant network. Furthermore, the special awards of the JIPM’s (Japan Institute of Plant maintenance) TPM Award were used as guidance. The project team was able to use the high level of motivation with which the plants' workforces competed against each other in a sporting competition when starting the digital transformation: for example, when planning the digitalization of existing OPEX tools or in the "custom-fit" selection of use cases according to the different digitalization needs of the plants.
Audit processes and communicate results!
In the OPEX programs, the company already carried out audits to check whether methods and technologies "took hold", e.g., in the more efficient processing of "commodity products". At the same time, the management used regular employee surveys to sharpen its picture of the issues, hurdles, and improvements at the workplaces in the lines and in logistics. The results of these surveys were published internally, which led to binding and more open communication. This strengthened an appreciative, trusting culture of discussion as a further valuable basis for future changes.
Clear objectives and an internationally strengthened corporate culture simplify the path to digital excellence.
Orientation towards realistic objectives
In the project phases described above, much more than a strategic target image was created. The company's management received a concrete action plan ready for decision-making and implementation for the digital transformation of the selected pilot plants in four years. EFESO identified best practices for digitalization from comparable food production facilities, used the GAP analysis to show where action was needed - and quantified realistic key figures as "targets" for the improvement steps in the subsequent implementation phase.
This stringent focus on results is a key feature of EFESO's approach. This not only enabled the Group management to communicate a clear, globally adaptable digital strategy to all stakeholders. As the potential impact on productivity and efficiency results and sales was quantified for all digital initiatives and use cases, management had a solid tool for monitoring and managing success during the implementation phase.
In addition, EFESO aligned the project results with a seamless transition to operationalization. The chocolate manufacturer received a "Smart Factory" target image that outlined the next elements such as building the IT infrastructure around a Cyber Physical System (CPS). At the same time, the company strengthened cooperation both within the plants and in the global plant network during these initial transformation phases: a traditional knowledge culture with "silo" structures gave way to an open culture in which best practices are shared and jointly developed. All in all, the chocolate manufacturer was ideally equipped to increase the performance of its plants and achieve "digital excellence" at the same time.