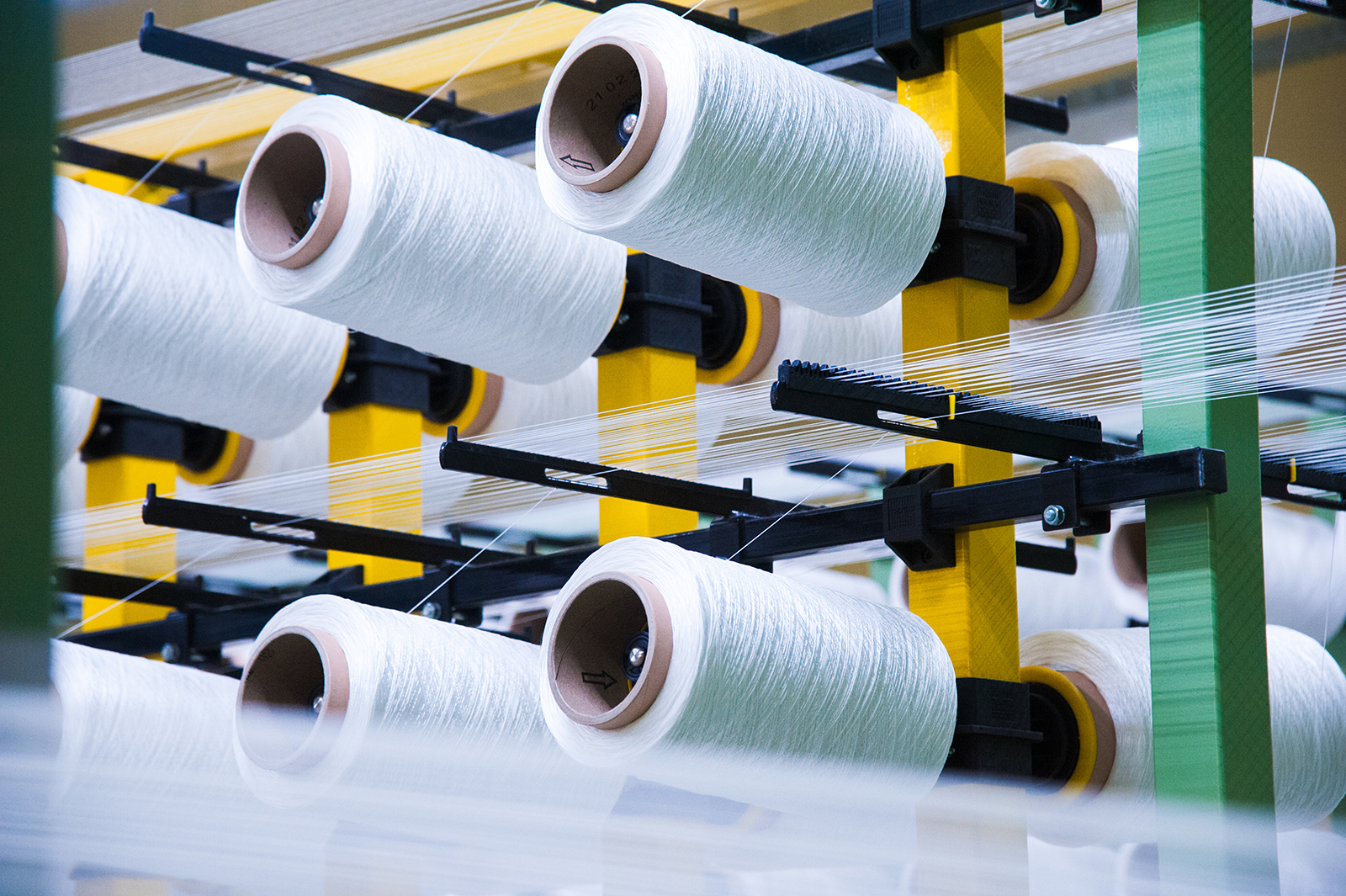
BLUEPRINT FOR THE SUSTAINABLE FACTORY
"How a global textile industry leader is developing a flagship factory for environmental and social sustainability in Bangladesh."
The textile and apparel industry employs more than 60 million people worldwide, especially in developing and emerging countries. In many places, however, production conditions are characterized by long working hours, low wages, a lack of occupational safety and environmental pollution. International standards and laws such as the European Supply Chain Act or the Corporate Social Reporting Directive (CSR) are intended to help improve the situation on the ground. Some companies are even going one step further and setting new standards themselves for forward-looking, sustainable production.
Challenge
A global textile supplier is planning to build a new production facility in Bangladesh. The plant is intended to be a touchstone for the company's sustainability strategy and serve as a model for other production sites in terms of taking social and ecological factors into account.
MOREEFESO solution approach
As a sparring partner, the on-site project team conducts a comprehensive analysis and evaluation of the current planning status and compares it with benchmarks and state-of-the-art solutions to identify hidden potential for more efficient processes, more sustainable use of resources and higher workplace attractiveness.
MORELessons learned
Comprehensive transparency and measurability with regard to emissions, resource consumption and the associated financial impact are key prerequisites for being able to target sustainability measures and continuously develop them further.
MOREEFESO success model
In order to make factory planning both environmentally and socially sustainable, a holistic approach that combines sustainability aspects with digital technologies and operational excellence is a key success factor.
MOREProof of concept for tomorrow's sustainable production
An American supplier company for the textile industry wants to break new ground in planning its production site in Bangladesh. Together with EFESO, the company is developing a concept for ecologically and socially sustainable production on site. As a leading supplier to the textile industry with around 70 locations worldwide, the company is aware of the signal effect of its actions. Therefore, the management wants to take a pioneering role in the industry with a consistently implemented sustainability strategy. As a lighthouse project, production in Bangladesh is to serve as a model for sustainable production - both in terms of ecological aspects such as CO2 emissions and water consumption, as well as aspects such as occupational health and safety.
For the company, the project is of fundamental strategic importance. The aim is to integrate digitization, automation and sustainability and thus create a proof of concept for the production of the future at the Bangladesh site. Expectations for the project are high: It is seen as a touchstone for dealing with rising labor costs in Asia and increased demands on supplier companies.
The plant is a touchstone for the sustainability strategy and a blueprint for all production sites
Interdisciplinary analysis, holistic optimization
As a sparring partner, EFESO supports the customer in reviewing factory planning for sustainability aspects, identifying optimization opportunities and jointly developing ideas for sustainable production and the factory of the future, which can later be incorporated into the Blueprint. This involves both internal processes such as logistics and material flow and the optimization of the factory layout with regard to integration with suppliers and customers.
The entire site is screened for ecological and social optimization potential
To this end, the project team conducts an on-site assessment of the initial situation and the planning status over a period of several days. Together with the customer's management and site management, the experts put assumptions and concepts to the test and compare them with benchmarks and state-of-the-art solutions. In this way, previously hidden potential for leaner processes, more careful use of resources and more attractive workplaces can be tapped in a short time.;
The Future Factory
Typical elements
Examples of sustainable factory design:
- A site-specific challenge is that the factory building is to be constructed and commissioned in two phases, which has a massive impact on operational processes. A building initially used as an external warehouse is to be integrated directly into production as part of the site development. Iterative revisions of the production layout and simulations of current and expected material flows will ensure that the building is used in the best possible way in all phases of the project - both in terms of energy efficiency and with regard to advancing automation.
- In addition, it becomes apparent that the previous planning leads to critical bottlenecks in the logistics, which prevent possible efficiency increases with increasing production. As a solution, the concept of using a small, fast and energy-saving special elevator ("Pallet Shooter") for the transport of transport pallets in addition to a large freight elevator was developed. Furthermore, this can create a logical material cycle within the factory.
- The large machines with which the company produces in turn generate heat that must be dissipated. The cooling units required for this have so far been located inside the factory. A holistic view shows that the optimal location for the cooling units is outside. This not only improves the company's energy balance, but also creates a pleasant working environment.
- In addition, it is apparent that the strategic scope and complexity of the project was not fully taken into account when setting up the team. The solution is a local team that is equipped with the appropriate competencies and project responsibility and is fully dedicated to the implementation of green production - and receives support from headquarters and other production sites in order to be able to implement the best practices that already exist in the company.
On the one hand, the insights gained are used to optimize factory planning on site. On the other hand, they serve as input for the blueprint for the design of future production sites worldwide. This enables the company to set new standards - and at the same time gives it massive leverage to translate more sustainable production at the Bangladesh site into long-term competitive advantages on a global scale.
With the results at the Bangladesh site, the factories of the future are being created worldwide
Lessons Learned
The project provides insights from which companies in other industries can also benefit. These include:
- Numbers are the key to the success of sustainability strategies. If the connection between emission reduction and cost savings, for example, becomes tangible, management and stakeholders can actively support the measures. That is why digitization, and sustainability go hand in hand. Because only in digitized production can sustainability performance be continuously measured and communicated.
- An understanding of sustainability that takes social and ecological aspects into account helps to improve production conditions both for the environment and for employees. In this way, the company can not only exploit economic potential, but also fully meet its special social responsibility. This also has a positive impact on employee retention and the search for new talent in times of labor shortage.
- Sustainability in industrial production is an interdisciplinary task. To achieve effective success, companies need a holistic view of sites, technologies and supply chains that takes into account sustainability thinking, digitalization and operational excellence. This perspective is created through exchange with experts and the involvement of, suppliers and customers.
Transparency and an interdisciplinary perspective that integrates social and ecological aspects are key success factors
The right time to build sustainable production is now. The pressure from scarce resources, critical end customers and stricter regulation is increasing. Our example shows how a company is rising to the challenge and expanding its leadership position through a consistent focus on sustainability.
If you also want to implement Sustainable Production in your company, talk to our experts now.