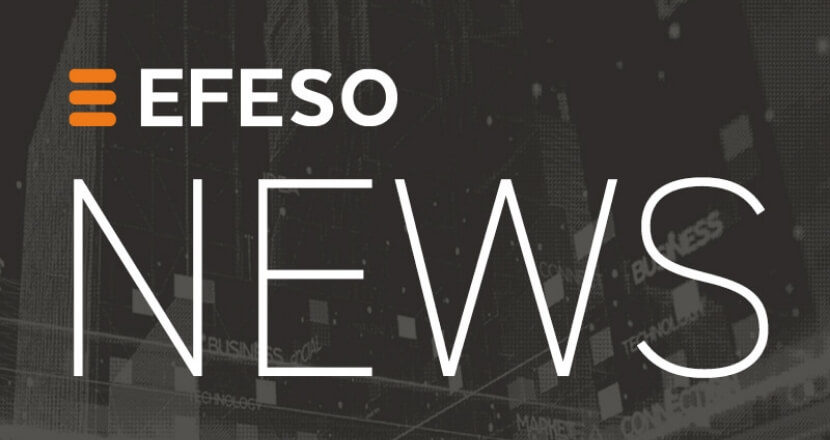
Review of the Training Day 2020
Review of Training Day 2020 with Tayfun Kaymakci, Head of Learning Campus, EFESO
Articles and interviews on current trends, technology and industry challenges, information on our consulting services, seminars and events as well as company topics:
Here you can find out what drives EFESO.
A natural growth of culture and technology is no longer possible. The dynamics of transformation must be actively controlled.
Traceability in focus: Digital initiatives in the process industry.
Increased resilience through data analytics – the challenges of effective data management in the Smart Factory exceed technical requirements out.
Digital shop floor management or agile methods in R&D eight impulses for the implementation of the Smart Factory.
Technologies and application scenarios, that are on their way to intelligent factory.
Toasters and refrigerators are transformed into “smart products” that will be controlled by Alexa and Siri in the future. A manufacturer of household appliances realizes: Three years from the first idea to the finished product are too long for that. He consistently upgrades his development team with ROI.
In the search for suitable cooperation models, companies often rely on individual methods and overlook the fact that they have to transform their organization sustainably - a guide to change.
Due to the increased complexity, the processes in product development have become more time-consuming and costly. At the same time, new technologies are speeding up processes considerably - insights into the race for efficiency.
Hardware and software development follow completely different development cycles. Synchronizing them is one of the greatest challenges of smart product development. A new control model provides a remedy.
Over the next 10 years, 90% of industrial products will have a software component. Most development departments are not prepared for this today.
Inventories are expensive - but at the same time they ensure flexibility. If you want to save costs and ensure high delivery reliability at the same time, you therefore need a systematic approach to dealing with inventory costs.
For a long time, industry 4.0 was regarded as a strategic lighthouse project. In the age of volatile markets, the “Return on I40” is now coming more and more to the fore. We show you how industry 4.0 makes a direct contribution to cost reduction.
A specialty chemicals group must improve its plant availability in a global plant network. The ROI Maintenance Excellence Program provides a fast acting approach.
Organizational structures that have grown or developed through acquisitions usually offer enormous optimization potential. To lift it, the organization often needs to be rethought from scratch.
The more complex the manufacturing environment, the more difficult it is to identify potential cost reductions. New search methods help to identify them.
The problem is not the crisis, but the uncertainty that precedes it. The ability to quickly adapt to volatile markets thus becomes a decisive competitive advantage.
Cultural differences between global locations can make it difficult to implement global standards. A ROI project shows how gamification approaches can counteract this.
When lean projects are rolled out globally, one thing counts above all: speed. Against this background, agile methods enable fast scaling.
For complex products with a high variety of variants, stand assembly is still often the method of choice. The example of MAPLAN GmbH shows how things can be different.
On-site management is a central Lean Management instrument. Supported by digital technologies, it becomes a springboard for industry 4.0 deployment in the enterprise.