SMART FACTORY & ADVANCED MANUFACTURING
The factory has always been at the centre of optimisation and innovation approaches in the manufacturing industry. The use of IoT or Industry 4.0 technologies promises to take processes and organization of the factory - the Smart Factory - to a new level. The following elements have proven to be target-oriented:
-
The core of the Smart Factory is the consistent use of data. Through sensor technology and networking, data is continuously collected that increases transparency and, by this alone, productivity, makes knowledge available and enables analyses and forecasts. At the forefront of the evolution of data use are autonomous systems that can control and decide independently of humans.
-
Lean Digital means significantly increasing the effectiveness of the proven principles of lean production through the intelligent use of real-time data. Instead of - for example - conducting one-off SMED workshops, the data of all set-up processes is continuously recorded and tracked, deviations in positive and negative aspects are made immediately transparent and thus performance is further increased.
-
Digital Shop Floor Management in the Smart Factory enables the processes to be controlled on site in real time. The core element is a consistent visualization of the current KPIs and deviations. In addition, the employees are supported by a consistent incident and action management as well as digital support for problem analysis. This ultimately leads to a significant acceleration of the problem solving speed and quality on the shop floor (faster PDCA) and thus to significant improvements in OEE and quality. With SOLVACE, ROI-EFESO has its own software package that has proven itself in the worldwide roll-out of global corporations.
-
The real-time control of production and quality (Real Time Production Control and Real Time Quality Control) allows the real-time recording of central process parameters and continuous comparison with sample values. This enables countermeasures to be taken within milliseconds, which leads to a significant reduction in rejects, lower quality costs and the prevention of machine damage, for example. Lean and Industry 4.0 are therefore not a contradiction in terms, but Industry 4.0 leads to a new leap in productivity based on lean.
-
Predictive Maintenance combines statistical forecasting models with sensor technologies to dramatically reduce costs by ensuring that maintenance is performed exactly when it is needed and avoiding production stops due to total downtime. In addition, the analysis of operating data and load scenarios allows an optimal allocation of production resources and the avoidance of idle or overload. At the same time, predictive maintenance approaches can be combined with condition monitoring systems for permanent monitoring of particularly critical elements, which allows high machine availability at significantly reduced costs.
-
Advanced Manufacturing is the collective term for new production technologies such as additive manufacturing, cobots, AGVs, etc. Assistance systems in the Smart Factory relieve employees of physical tasks by means of semi-autonomous or autonomous transport and robotics systems or networked digital solutions such as apps, or augmented reality applications such as Smart Glasses.
-
In the Smart Factory, the decentralized organization can be seen in the dissolution of the hierarchical pyramidal structure in favor of a network oriented to the value-added process. This transformation reduces the control effort and allows a largely autonomous coordination of the individual network elements and production-relevant software solutions such as ERP, MES or PPS. The basis for this is the use of M2M, RFID or Smart OTS technologies and the equipping of machines, workpieces and production rooms with sensor technology.
-
What makes the "intelligence" of the Smart Factory? A central point is a long-term oriented IT strategy and a scalable IT architecture. Individual digitization solutions can usually be implemented very easily. The challenge, however, is the economic roll-out. After all, the Smart Factory generates immense and complex data volumes. Only those who master and control these data volumes with the help of scalable IT can also realize the economic successes that Industry 4.0 promises.
-
Leadership and qualification are of decisive importance in this context. Many roles change, new qualifications are required and new collaboration models must be learned. As in any other change process, fears arise. Managers must be prepared for the changes just as much as experts. ROI-EFESO's Learning Campus and ROI-EFESO Learning Factories offer a comprehensive, tried-and-tested qualification programme for this purpose.
-
The sustainability aspects of a modern smart factory represent an important design dimension. With the goal of a "zero-impact factory", various measures are implemented to reduce environmental impact, for example in the areas of energy and water consumption, pollutant emissions, material and operating material efficiency, waste management or the avoidance of operational disruptions.
-
Last but not least, factory planning and plant development must be adapted to the new possibilities. The gain in flexibility through digitalisation must not be offset by rigid layouts. Plant development should become more modular and flexible. Interfaces to partners and systems should be planned accordingly.
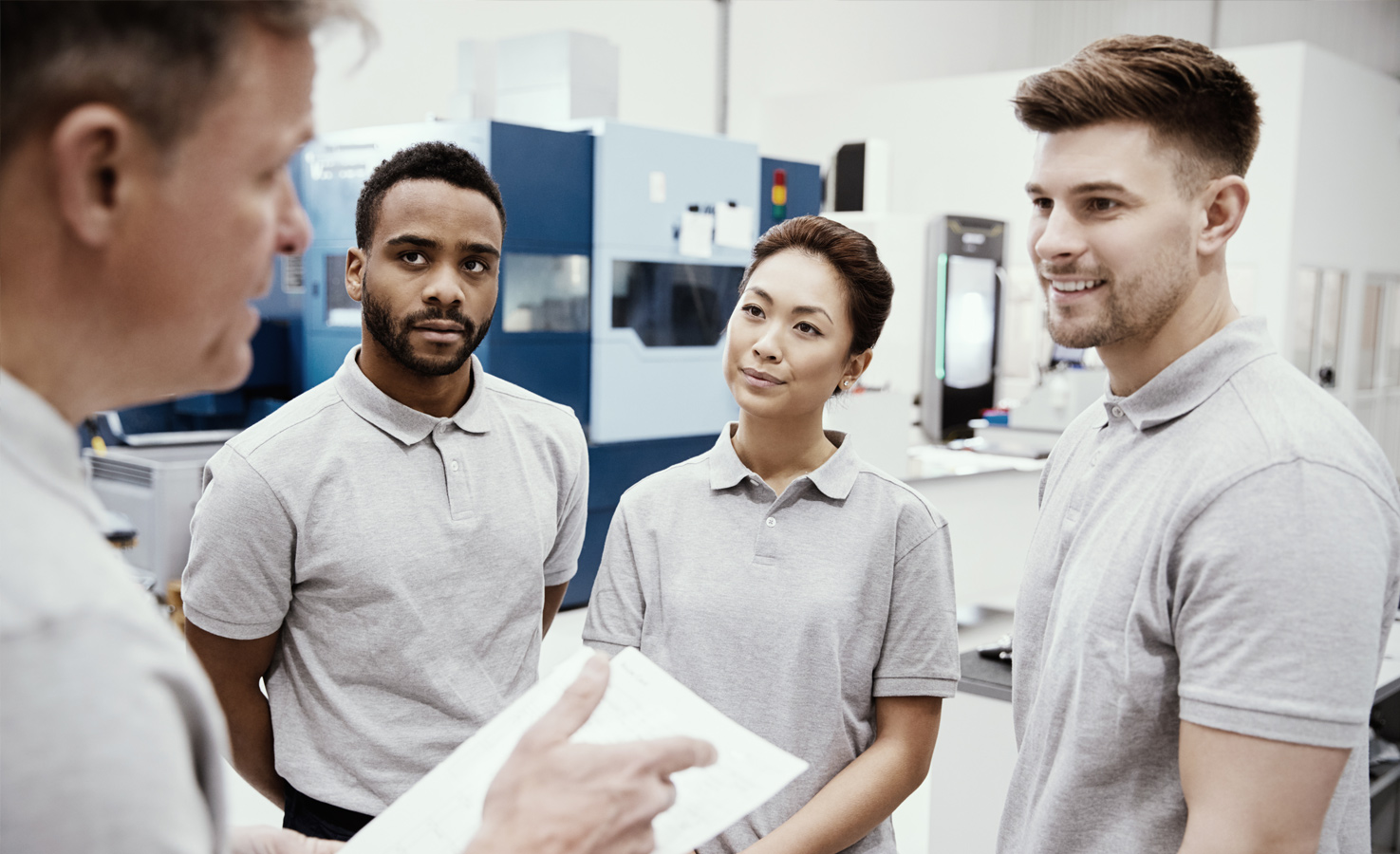
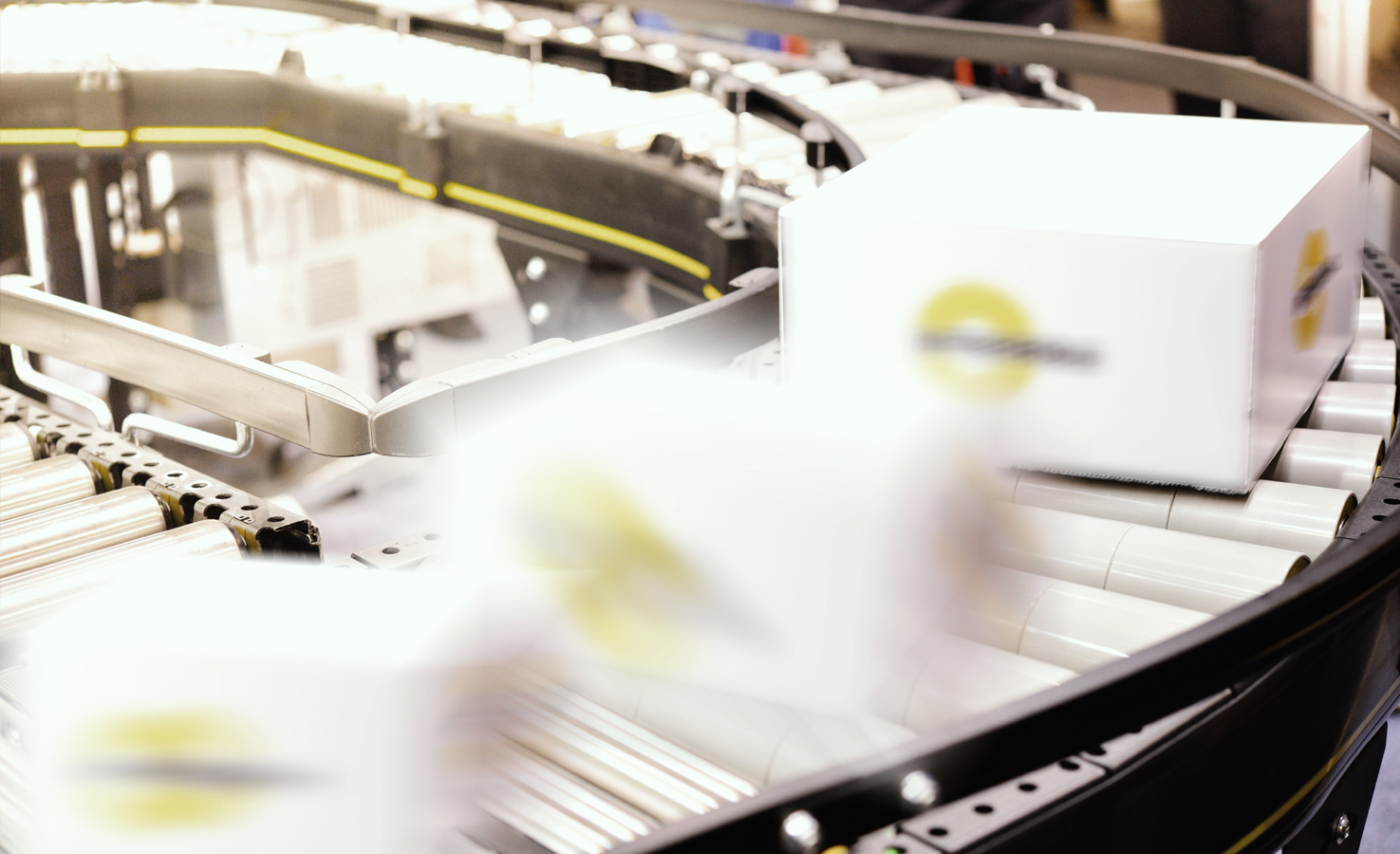
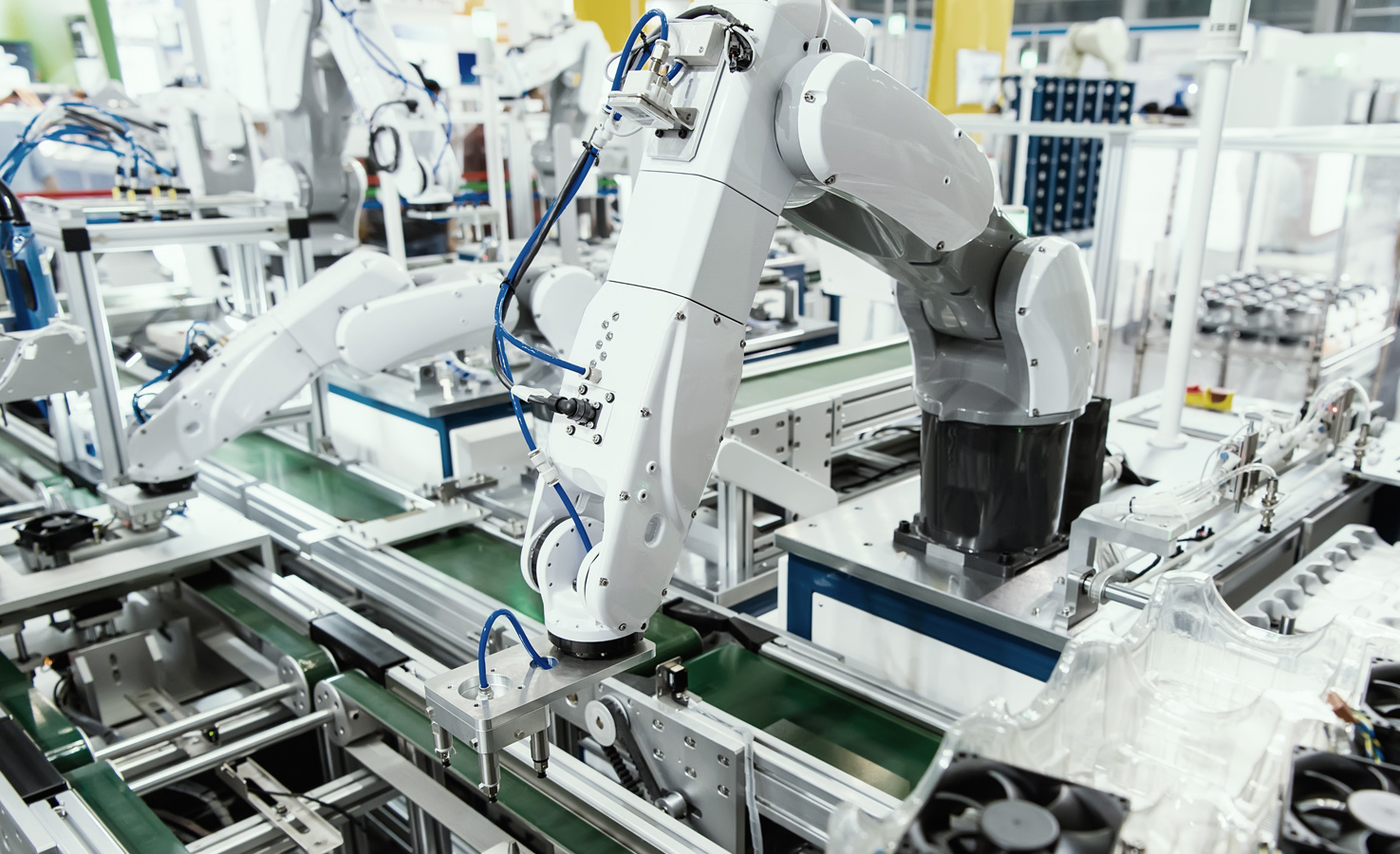
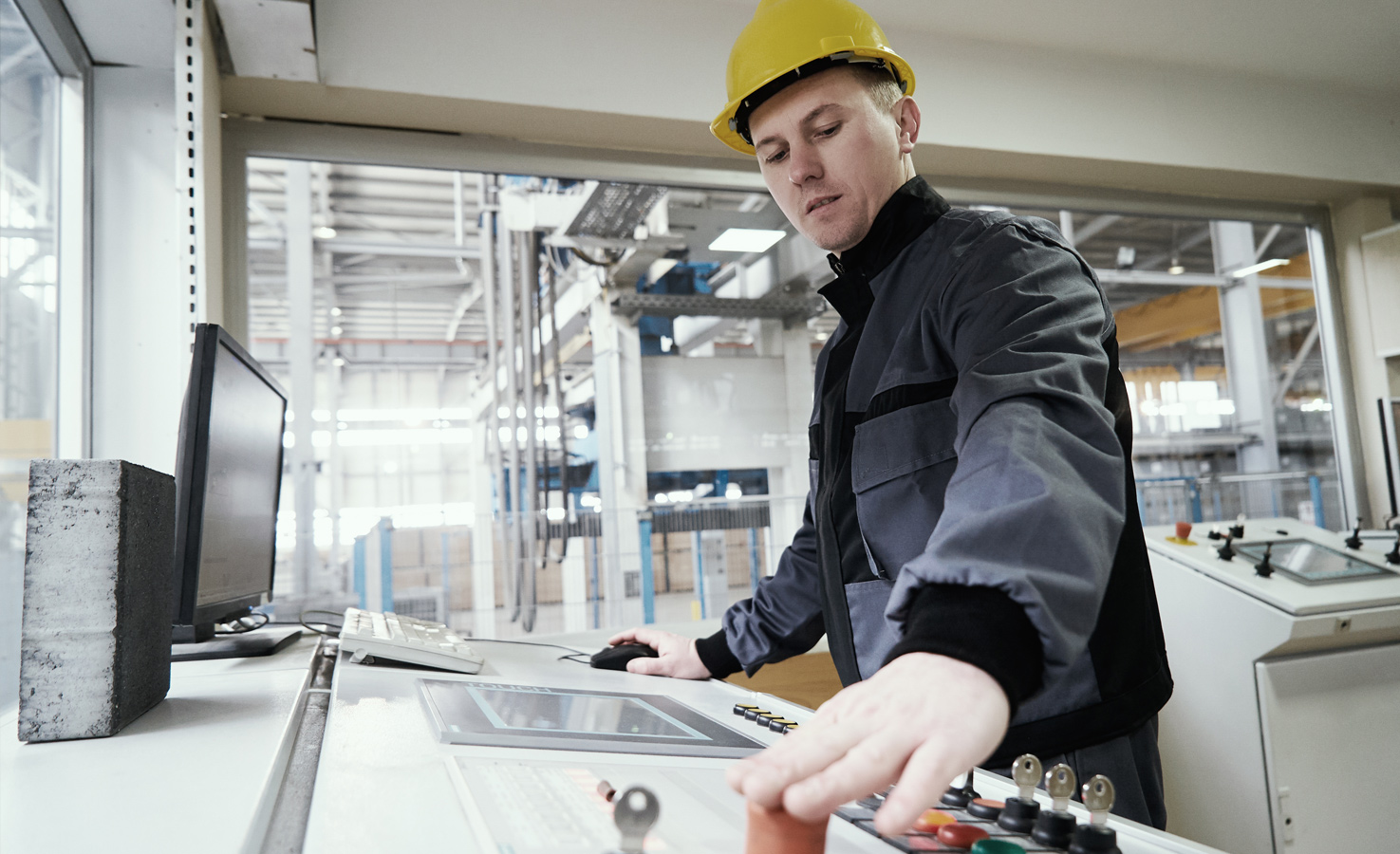
For more than 10 years ROI-EFESO has been developing and implementing Smart Factories worldwide. Extensive references prove our experience and expertise. Talk to us about it!