TOPICS & NEWS
Articles and interviews on current trends, technology and industry challenges, information on our consulting services, seminars and events as well as company topics:
Here you can find out what drives EFESO.
SILENT GUARDIAN FOR THE ENERGY SUPPLY
When martens explore substations, contact with several hundred thousand volts sometimes ends the flying visit quite drastically. However, the risk does not only lie with the marten. Wild animal damage at such a neuralgic point of the energy supply can lead to power failures or material damage and have costly consequences. Our remote maintenance solution prevents this by simplifying the management of maintenance activities in substations. In addition to uninvited guests, a specially developed camera system keeps an eye on weather conditions, plant growth, component wear and many other points to ensure the continuous operation of the plant.
Efficient use of scarce resources
This task is extremely demanding for several reasons. Through our control center in Berlin alone, our company is responsible for the operation of 65 substations whose maintenance conditions are very heterogeneous: The plants vary in age and more than two-thirds have been in operation for more than 30 years. The older plants in particular have little or no sensor technology for measuring machine or environmental data. Retrofitting individual IoT solutions here would be very complex, cost-intensive and difficult to integrate into a control system. In addition, the substations are usually located in remote, rural regions and must be maintained by highly specialized, i.e. rarely available, skilled workers. In this respect, too, limited resources must therefore be used as efficiently as possible, i.e. , as many measures as possible, such as lawn and plant pruning, should be carried out with other activities at a maintenance appointment. This in turn requires forward planning based on precise site information.
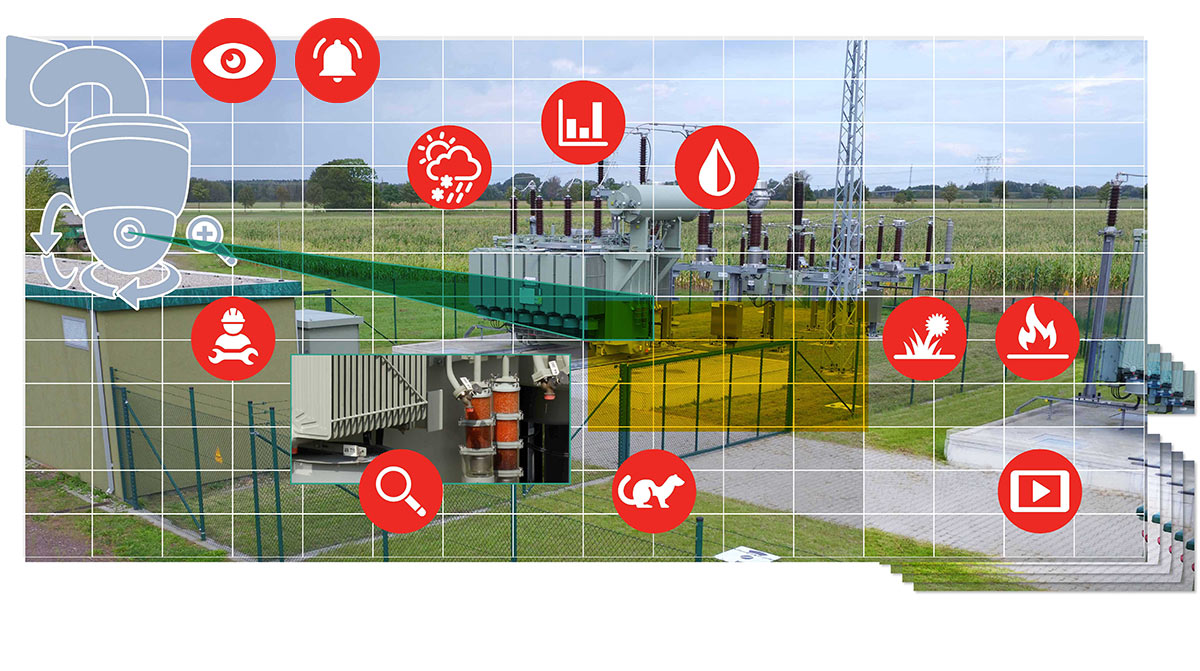
Risk zones at a glance - live and data protection compliant
To solve this and other challenges, we developed a system together with our partner Hesotech that monitors the plants 24/7 with a camera, documents all the necessary information and processes the images and videos into measurement data using computer vision. Depending on the event at the site, the maintenance technicians are immediately alerted or informed in good time about upcoming work.
Optimal configuration with digital system twin
The central highlight of the solution are the camera systems and the associated software algorithms. All information is merged in a digital twin (2D or 3D). The algorithms developed first enable us to calculate the optimal position for the cameras to be installed in the digital twin. After the system is set up, algorithms from image processing are used to implement various use cases for optimizing maintenance. The objects and parameters (limit values, confidence intervals, etc.) that the system is to monitor or evaluate are defined, e.g. counters, critical components, lawns, plants or access points to the site.
Precise control through high-end cameras
The camera periodically records the set monitoring points - in the pilot plant these are more than 3,000 physical points . It can cover distances of +150 meters and work not only in daylight, but also with thermal and night vision images. Another special feature is that the camera system only records the predefined points and hides everything else. If maintenance personnel are on site, the cameras are automatically deactivated.
Direct alerting in case of emergency
In surveillance mode, the system detects intruders such as wild animals and thieves as well as smoke. In these cases, it automatically triggers an alarm and sends push notifications to the responsible personnel. In the event of significant faults such as a fire, the alarm-triggering event is also transmitted directly with a live view.
In "normal operation", the system controls many other functions. For example, the permanent temperature monitoring of relevant components via the thermal imaging mode ensures that critical temperature developments are detected at an early stage and countermeasures can be initiated. Networked sensors collect further real-time data via a weather station and microphones, so that detailed information from fault messages or damage is available over time and maintenance cycles can be adjusted accordingly.
Failure analysis for predictive maintenance
The bundling of these functionalities is extremely advantageous for two reasons: On the one hand, a wide variety of systems can be "informed" about all essential control factors (temperature, humidity, vibrations, damage/wear) in one step, without having to install, network and operate individual IoT solutions for these requirements. On the other hand, the operational use and the "needs" of the plant can be visualized with the collected data. The maintenance team can access this information via a dashboard.
By the way, not only the condition of the plant and the events there can be assessed via the live view in real time. A "look into the future" is also possible. This is because the operating data from the control system can be linked with image recognition data in the digital twin to support error analysis and thus, for example, provide early warning of wear or increased plant growth in the plant.
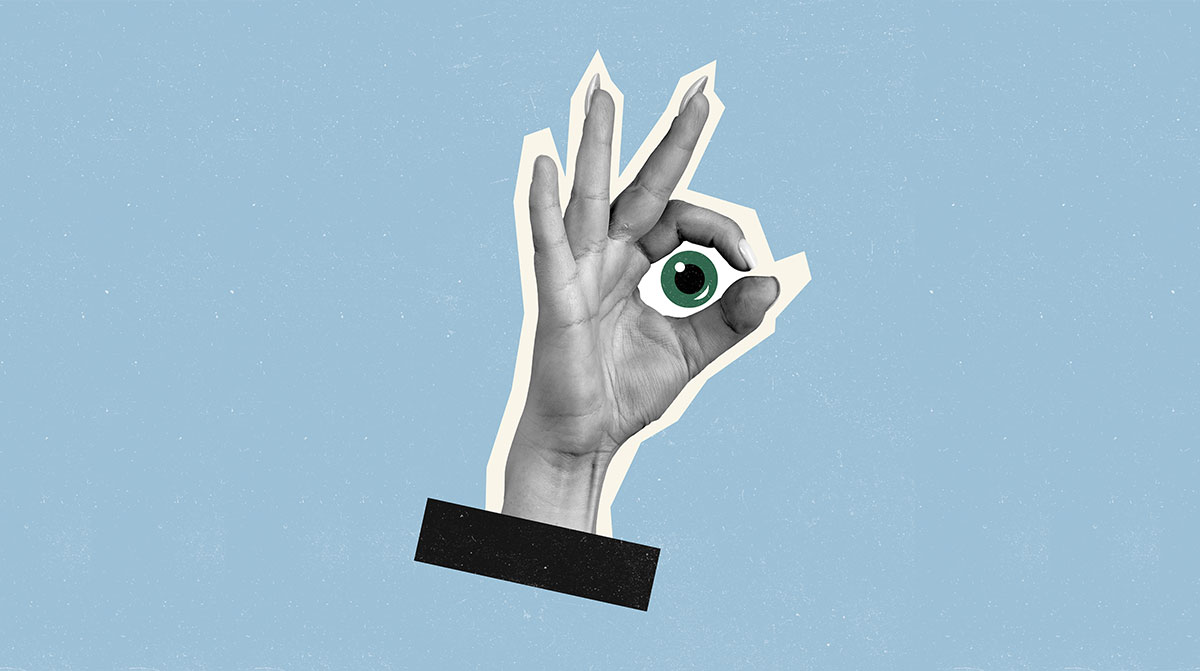
Falling costs already in the pilot project
The system is currently in operation at a pilot site and at another substation and is also to be used at the other plants in the future. Already in the pilot project we were able to reduce the operating and maintenance costs of the plant by about 15% p.a.. Thanks to the shorter response times in the event of alarms or damage as well as improved maintenance planning, downtimes have also been significantly reduced.
The approach of covering as many measurement and monitoring scenarios as possible with the camera as the one central sensor and "node" is proving to be very productive. However, future add-ons such as the installation and networking with vibration sensors in the plant are of course not excluded. They provide very good additional indicators that something is wrong, for example before smoke develops. And finally, anything that further reduces risks - for the plant operation and also for the marten - makes sense.
Field of application: Energy supply
Challenge
Improving substation operational management through predictive maintenance and repair.
Solution
Visual monitoring, documentation and analysis of the entire plant via an intelligent camera system that monitors the plant 24/7 and processes the images into measurement data.