TOPICS & NEWS
Articles and interviews on current trends, technology and industry challenges, information on our consulting services, seminars and events as well as company topics:
Here you can find out what drives EFESO.
LET´S PLAY LEAN
German overadministration, American freestyle and service by the rules in China. Cultural differences can be a real challenge when introducing global lean standards in manufacturing. With playful approaches, intercultural teams and local initiatives, ROI succeeded in overcoming these difficulties for a global automotive supplier.
The Group, with around 20 successfully operating plants in Asia, Europe and North America, employs around 10,000 people in operations. Cultural differences and extremely heterogeneous operational structures and processes at the plants made performance comparisons and cross-location knowledge transfer more difficult.
In order to tap value creation potential and promote exchange, comparable lean standards were to be introduced in the entire operations area. An international OPEX team should motivate those responsible to actively exchange ideas and anchor OPEX thinking processes at all hierarchical levels as early as possible. A key success factor was consistent local stakeholder management.
The OPEX measures were adapted to the information and communication conditions in the plants - “Think global, act local”. This was intended to dispel reservations about OPEX on the part of local employees.
With playful forms of learning and role reversal, ROI ensured rapid development of knowhow and structured operating processes that function internationally. Instead of standard presentations, a creative design approach was chosen to visualise OPEX-relevant information, which quickly led to a lively and fruitful dialogue between managers from China, Japan, the USA and Europe.
Plant managers, department heads and technical experts from all over the world met several times for operations conferences in order to experience measures to implement the OPEX target image in different roles with different tasks. Participants were able to “play through” various prototypes on the standard assembly line and experienced directly how the product change feels on the line and what concrete changes it would bring. OPEX market stalls illustrated the various main topics and increased the exchange of ideas. In order to sensitize plant managers to how early integration of operations can change the entire value chain, they jointly built a toy car at the OPEX meeting. The clou was that role reversal was mandatory. Colleagues from manufacturing, purchasing, development and sales exchanged roles, as did different nationalities. Practically relevant experiences could be experienced in a playful way, the benefits of OPEX were not an abstract requirement. Commitment at all hierarchical levels and control of the measures ensure lasting success.
ROI conducted telephone interviews with randomly selected employees to monitor the success of the measures in practice. Already after completion of the first project phase, it became apparent that the cooperation within the locations as well as the cooperation of all factories could be significantly improved. A monthly newsletter and regular “Town Hall Meetings” ensure the flow of information and accompany the upcoming change processes in the next project phase.
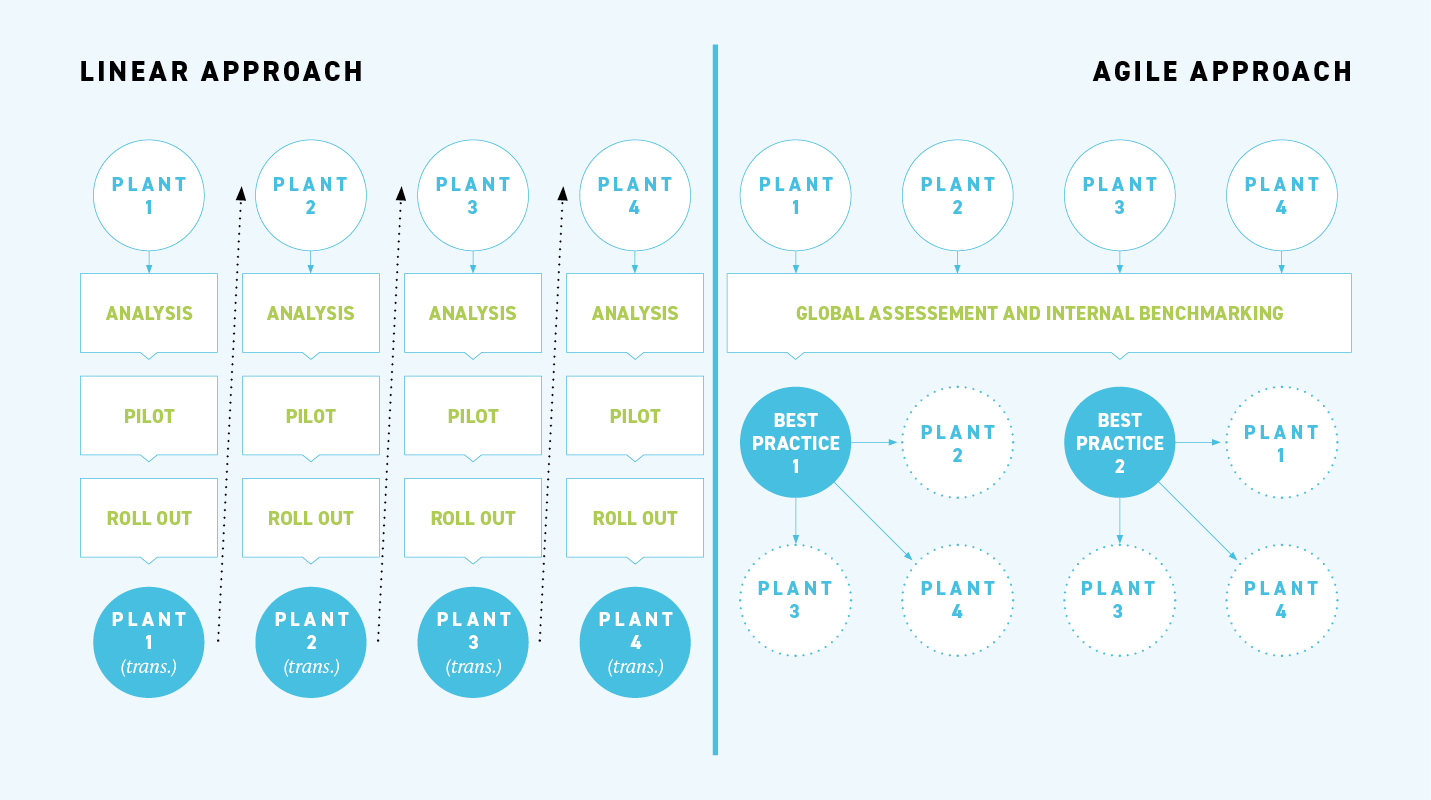