TOPICS & NEWS
Articles and interviews on current trends, technology and industry challenges, information on our consulting services, seminars and events as well as company topics:
Here you can find out what drives EFESO.
TARGET: IDEAL ONE-PIECE FLOW
With its electric and hydraulic power steering systems, Bosch HUAYU Steering Systems ensures that car and truck drivers can move their vehicles comfortably in traffic. The high-tech enterprise has the largest business scale and highest market share in its sector in China. At its plant in Wuhan, Bosch HUAYU manufactures electrical and hydraulic power steering systems and the key component worm and pinion with around 70,000 pieces in work in progress (WIP) inventory.
Five years ago, the plant launched a project with the aim of optimizing component production and coming as close as possible to the guiding principle of one-piece flow. Among other things, throughput times and flexibility were to be improved, for example by automating the manual movement of goods between workstations or by digitizing the previously paper-based data capture.
FITS: High-flexible planning with limited resources
Already well on its way, the project team had to deal with the constraints of the pandemic. During the COVID-19 breakout in Wuhan, the majority of business were obliged to close down. That resulted in a drastic reduction of direct personnel in the factory. Since some of the targeted technologies had already been implemented by this time, it was possible to maintain production with a severely reduced workforce and continue to fulfill customer orders.
This was made possible by FITS, an advanced planning and scheduling solution, which stands for “Flexible Intelligent Transportation System” and was initially concepted in the process of planning the worm single frame flow. The system should be able to capture real-time status feedback from each asset, enabling precise production planning. Furthermore, it should dynamically adjust the production task of each equipment according to the production planning and equipment state. Additionally, a dynamic change of the individual workstations should also be made possible. Therefore, the system had to have these properties:
- high-flexible production route planning with limited resources;
- accurate to the dynamic scheduling of each equipment;
- material transfer automation, single box traceability;
- real-time feedback of material information and real-time monitoring of equipment status.
This evolved into the FITS project: By using the core production scheduling system, based on RFID and MES structures of manufacturing systems, the whole production process was transformed from a traditional discrete planned manufacturing to an agile on-demand manufacturing. A set of five solutions has been implemented for this purpose:
Core algorithm & Advanced Planning and Scheduling system (APS)
The central element of the project is its “smart brain”, i.e. the software algorithm. The algorithm analyses customer needs and converts those with other demands into executable production tasks. It records each piece of equipment so that an optimization to the setup sequence in the material flow can be made in the shortest possible time. In combination, an overlaying APS system for real-time planning and scheduling is matching deliveries with unexpected production volatilities. In case of exceptions like machine breakdown or missing material, an automatic rescheduling is initialized: the production plan is updated automatically, the shop floor manager is automatically notified and only has to confirm.
Manufacturing Execution System (MES)
An MES developed by Bosch was implemented to record the data generated in the production process. Among others, the MES includes functions like tool-, quality-, order-, and energy management, light system control and manufacturing data analysis.
Automatic Guided Vehicle (AGV)
The FITS algorithm generates transport requests based on the real-time production status and material availabilities feedback by the MES data and sends them to an AGV dispatching system. The system executes the transport orders and thus independently transports materials, components and tools between the individual stations and workplaces. The individual AGVs have the functionality to adjust the height of their wings. This ensures transport to and from production cells of different heights. For the AGV, no floor guide rail or magnetic strips need to be laid, nor is it necessary to attach a QR code to ensure that minimal floor changes can be overcome.
Radio-frequency Identification (RFID)
Each transport rack (which holds 48 identical parts each) was equipped with RFID tags, and each production line was equipped with corresponding RFID readers. All process- and machine data is stored on parts-level via MES and synchronized with the RFID data. Of course, the (automated) setup of equipment also had to be synchronized with production program planning.
Human-machine interaction (HMI)
The electronic information visualization of intelligent manufacturing, namely the window of human-machine interaction, is the bridge of system diagnosis and monitoring. At present, the FITS project selects a hand-held terminal that can scan electronic tags to read information of suspicious materials, and conducts isolation, scrap or return processing on the corresponding interface. Mobile tablets are used as paperless office tools for on-site inspections and equipment adjustments. They are also connected to the wireless network to obtain and monitor the production status and the quality of parts.
How do you use Industry 4.0 technologies to make manufacturing more efficient – without creating new complexity? Jun Bao, Wuhan Plant Manager at Bosch HUAYU Steering Systems, calls empirical values.
DIALOG: Mr. Bao, what smart factory vision are you pursuing with FITS?
JB: We started the project with a few objectives that nicely outlined our vision. First, to plan the different quantity of the machines for different processes. For a continuous material flow, several pre-conditions must be ready. For example, for every machine we need to know its actual status, what type of component it is producing and the manufacturing progress. In simplified terms, it is IoT of each machine equipment.
Second, since we want to have a one piece flow of the component, we needed to define a standard unit. This enabled us to adjust the components like this. So, we defined a standard lot for this component, which is 48 pieces. We put it in a standard packaging that can be accepted by every machine. For each lot, we know in real time where it is, what’s the manufacturing progress and how many of the individual parts have already been processed.
Third, we had to consider where in the process it would make sense and be profitable to implement the targeted solutions. So naturally with the ideal one-point flow, we will not have any additional non-value operation, like moving components. So as a precondition, those components should move by themselves or automatically. Therefore, we need to find a way to move a single lot from one station or from one machine to another.
DIALOG: But every machine is in every time or sometimes in a different status. How did you manage this complexity?
JB: This was the fourth precondition: we needed a kind of a data analytics “brain” knowing the status of the components and the status of the machines. And it should also be able to give dynamic orders to each AGV, to each machine and dynamically telling them what to do or what you need to do now and what you will do next. Our FITS algorithm can do that – and even more. He is dynamically receiving the feedback of the machine. If suddenly one machine broke down, FITS informs us directly and makes suggestions how to react, e.g. switching to other machines in a certain time frame.
DIALOG: Besides the technologies used, what made your project successful in the end?
JB: The teamwork and the development of the competences. In the past, team members in the manufacturing industry mostly had different roles and backgrounds. These roles are evolving by the request of multi understanding.
However, new ideas are often developed behind the boundaries of your own discipline! For example, by concepting and running FITS we realized how important it is, that a process engineer needs to have IT knowhow as well. A maintenance engineer needs to know how AGV is running, how to maintain an AGV and how to market a new one. This is naturally happen and if you want to implement as much useful IoT solutions as possible, you need to intentionally notice who is growing to which of this mountain knowledge. It is important to give the chance to your teams to grow in this way. By doing that continuously, you will have not only one highly motivated team, but more and more teams who can plan, implement, and evolve an industry 4.0 solution as well.
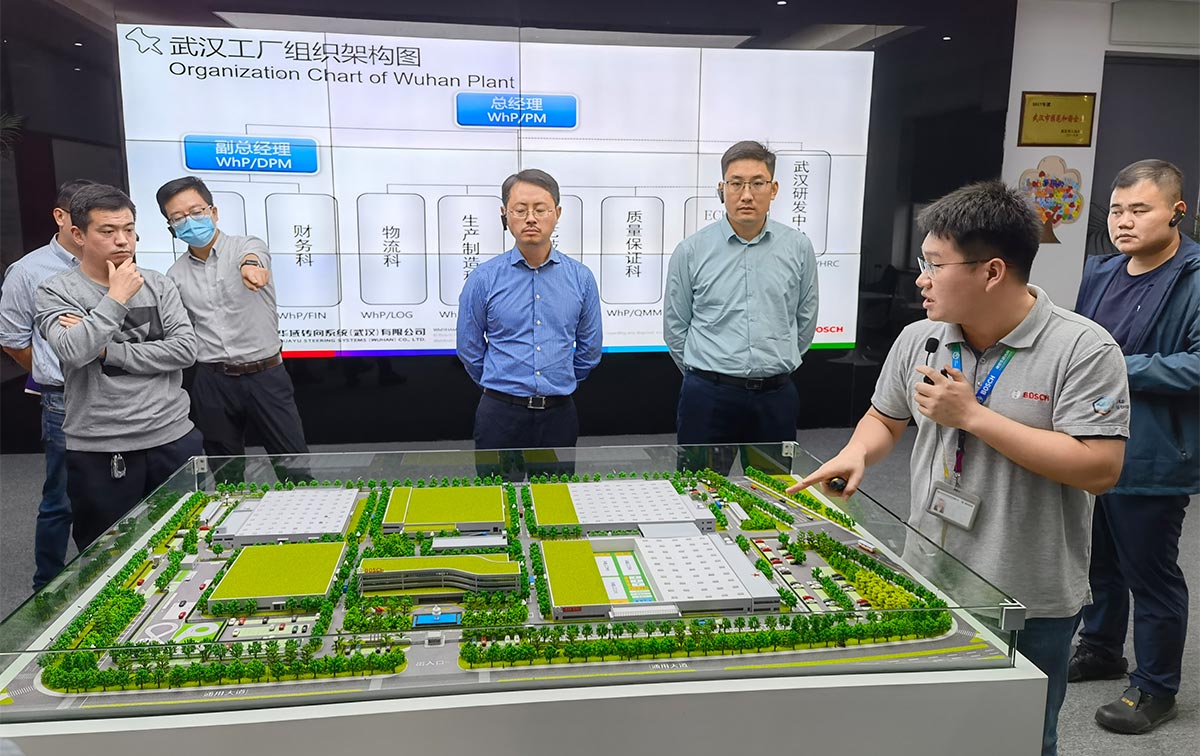
Field of Application: Automotive Industry.
Challenge
Transforming the production process of car components from traditional discrete planned to agile on-demand manufacturing. Due to the COVID-19 lockdown, the project team also had to manage a drastic reduction of direct personnel from sixteen to two operators.
Solution
Conception and implementation of “FITS”, a transportation system to optimize the material flow. With the combination of five core modules (MES, APS, AGV, RFID and HMI), FITS transformed the production flow from dedicated production lines to a modular production system. Adjustments during the lockdown also led to more flexible and highly automized processes that enables the plant site to react quickly to short-term interruptions.