TOPICS & NEWS
Articles and interviews on current trends, technology and industry challenges, information on our consulting services, seminars and events as well as company topics:
Here you can find out what drives EFESO.
3D printing: Strong Momentum
Fresh impetus for the future development of additive manufacturing
Additive manufacturing is fascinating in particular because of the virtually infinite range of products. Apparel, mountings for jet turbines, automotive bodywork components, titanium implants for human bones and many other innovative products are impressive proof of the range of possible applications in almost all areas of life. However, anyone wishing to understand the development potential of the technology should direct his gaze beyond the products range to the extensive ecosystem that supports 3D printing. Factors like design & order development and workflow management have a direct effect on the evolution of 3D printing, while factors like standardization have an indirect effect (see figure on p. 4).
“As in any ecosystem, also in additive manufacturing the complexity and momentum of many elements make it difficult to predict the next stage of development. However, some trends are becoming more noticeable,” says Anselm Magel, expert for 3D printing at ROI Management Consulting AG. “Simulation software, for example, is playing an increasingly important role for melt pools and the process of powder bed-based laser melting. Thanks to the software it is possible to simulate tension, distortionand the microstructures of metal parts on a computer and as a consequence eliminate errors long before manufacture.” A Other core trends include topology optimization of functional parts or the new technology of electrolytic metal powder production, which is significantly more cost-efficient than gas or plasma atomization that predominates nowadays. The standardization of a new file format by the 3MF Consortium intended to replace the outdated STL format is also having a positive effect.
High Development Potential: Metals
“Besides the currently dominant polymers, metals are the key raw materials for the next development steps of the technology,” Magel emphasizes. “Five process variables will determine the design of the production process: metal powder characteristics, jet performance, the speed at which the jet travels, the layer height or speed of material feed, local geometry and the temperature of the parts at the melting point.” Here, the switch from empirical to simulation-driven additive manufacturing becomes essential. Process simulation helps modelling the structural characteristics of the selected metal like heat build-up, displacement, residual tension and crystalline structure.
“Also exciting are the possibilities of in-line quality and process monitoring and control that will soon be available. Metal processing additive manufacturing systems are currently not fitted with any sensors, or only with thermal elements in the thermal chamber, and products are made using a linear feed method. In the next few years it will be possible to measures the temperature, the precision of the geometry and the state of the powder bed before and after the melting process, i.e. during the production process. These data can then be used to correct the construction job during the process, vastly improving quality and production speed,” Magel explains. In future, Magel expects to see repeatable production processes, reproducibility on other equipment and high-quality production results as a consequence of the interplay of future innovations, like in material powders or in manipulating material microstructures and porosity. We can also assume an exponential increase in the speed of manufacturing 3D-printed products. “Optimizing manufacturing process variables will make it possible to achieve four- to five-fold growth in production speed for metal process systems – and, depending on the object and size of the series, the decrease in costs per part is likely to be in the double-digit range.”
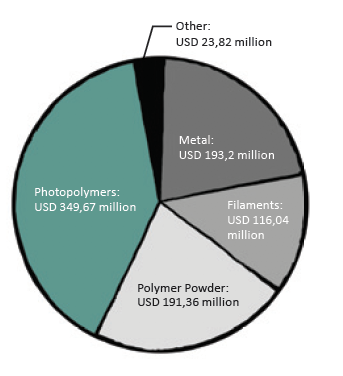