- Selection of suitable regions (factor costs, labour market and supplier structures, infrastructure, regulatory framework, economic development).
- Search for suitable properties (land, building developers, basement properties).
- Personnel recruitment for the planning and development phase.
- Technical due diligence of land and sites for technical feasibility and risks.
- Brownfield / greenfield projects: differentiation and specialized approaches for existing sites versus new builds.
Consulting factory and logistics planning
A look at many locations shows that plant structures survive for a long time. It is therefore particularly important to proceed with prudence and professionalism and to involve the right partners when planning a factory - be it a new building or a conversion.
In the beginning is the idea. We are happy to share with you our ideas of a factory of the future. From our point of view, layout and infrastructure must enable efficient flows, promote cooperation between employees and support the joy of creating value. To ensure that a factory is still one of the best in 50 years, we rely on the following key elements:
- Modular, so that you can grow and properly integrate value creation partners
- Flexible, because products and technology change
- Optimal in terms of material AND information flow
- Smart and digital
- Energy Efficiency, CO2-neutral and resource-saving
Before the excavators roll, the ideas must be developed into robust concepts and concrete layouts. This is not possible without the involvement of stakeholders, who demand coherent concepts and a convincing business case based on several comparative scenarios. Here it is important to work out the potentials on all levels in concrete terms and to evaluate them in a comprehensible way.
Sustainability aspects play a major role in modern factory and logistics planning. Under "Zero-Impact-Factory", various environmentally friendly measures are implemented, ranging from the reduction of energy and water consumption, CO2 and VOC emissions to waste management and soil protection.
In order to achieve a high level of planning efficiency and to manage risks in the course of the project with foresight, an iterative and agile approach is recommended. It is carried out according to the following guidelines:
- from the central (value-added process) to the periphery (outdoor facility)
- from the rough (general planning/plant structure planning) to the fine (workplace design)
- from the ideal (Greenfield) to the real (Brownfield)
This ensures that unnecessary discussions at the beginning (e.g. about the colour scheme of the offices) do not slow down the overall process significantly. Experience has shown that the desires of all those involved are great when it comes to new planning and replanning. We take great care to ensure that the planning focuses on the essential issues, especially those that affect the building structure, investment level and potential.
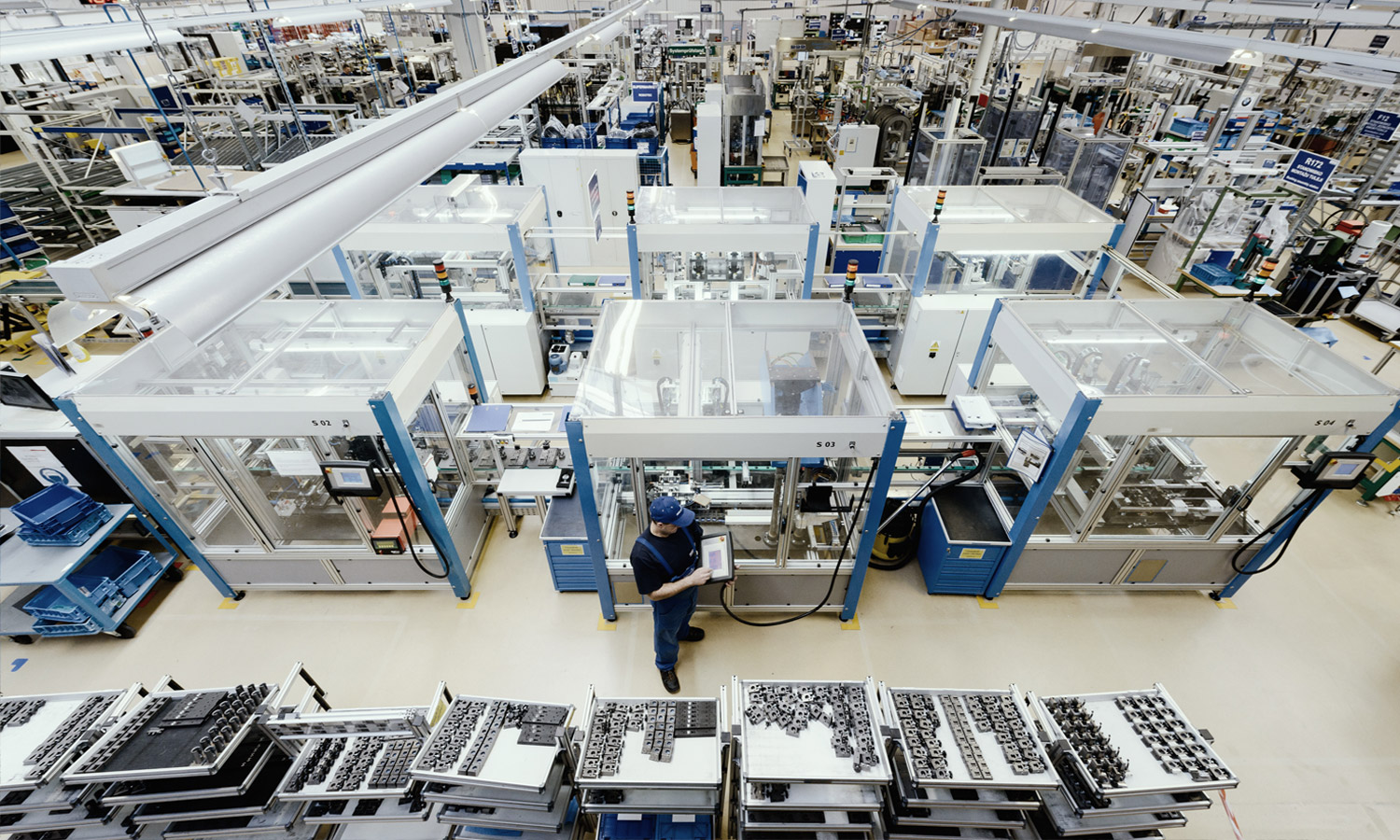
EFESO supports you from the first planning idea to the start-up of the factory or logistics centre. This ranges from strategy development and site selection in the run-up to the entire project implementation to the onboarding of local suppliers in the ramp-up phase. Our range of services includes:
Location search and selection
Production and logistics concepts
- Future-oriented value flows in production and assembly.
- Line and plant planning.
- Material supply and disposal systems.
- Storage and transport systems.
- Preparation of tenders.
- Supplier selection and integration.
- Planning of inventory management concepts.
- Dimensioning and technology integration: detailed dimensioning of production facilities and integration of specific technologies.
- Infrastructure and supply planning: planning and integration of energy, water and supply systems in production.
- Material flow and logistics simulation.
Smart Factory
- Horizontal integration from product design to delivery / paperless factory.
- Advanced operator support, cobots and exoskeletons.
- Digital visualization in the factory.
- Automated storage and retrieval systems / Smart Automation.
- (Partially) autonomous transport of materials and assemblies.
- Open / flexible office concepts.
- Requirements on the IT infrastructure.
Scenario and layout planning
- Master planning scenarios and expansion options for locations.
- Design and detailing of the overall layout: greenfield and brownfield, rough and detailed concept.
- Area and spatial planning for value and support areas, infrastructure, office spaces, social areas and outdoor areas.
- Determination of the building structure.
- Digital planning in 2D and 3D.
- Scenario evaluation: economic efficiency calculations and concept simulations.
Implementation support
- Tendering, supplier selection and awarding.
- Coordination and support during production ramp-up.
- Qualification concepts and training for employees and suppliers.
- Project management and project controlling.
- Claim and risk management: processes for actively handling project risks and claims during the construction phase.
- Handover management: clear processes for handover and ensuring operational readiness after completion of the construction and realization phase.
Sustainability & Zero Emission Factory
- Energy-efficient technologies and production facilities.
- Sustainable supply concepts.
- Planning of low-emission buildings and infrastructure (CO2-neutral).
- Energy recovery concepts.
- Circular economy.
- Building certifications according to international standards (DGNB, BREEAM, LEED).